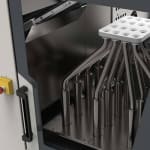
Maximum integration with a minimal footprint
Highly integrated, compact production cells minimise the system footprint and increase area productivity. These aspects really pay off in the cleanroom. Engel further developed the stainless steel pipe distributor for the cavity specific handling of small injection moulding parts, so that the handling system now fits completely into the expanded safety gate of the injection moulding machine. At Plast Eurasia this extremely compact solution will be demonstrated using the production of needle holders for 1 ml safety syringes as an example.The precision parts will be manufactured from polystyrene on an Engel e-victory 170/80 injection moulding machine equipped with a 16-cavity mould by Fostag Formenbau (Stein am Rhein, Switzerland), taken off the mould by an Engel viper 12 linear robot and transferred to the distribution system. To ensure batch traceability down to the individual cavity, the filigree parts will be packed in cavity-specific bags. For this purpose, the 16 bags are hung in a cart located directly beneath the pipe distributor. Individual shots can be extracted for quality inspection purposes.
To ensure fully automated cleanroom operation, two carts are alternated in sequence, with a buffer system enabling the automated exchange during on-going production. All the peripherals for this are integrated into the CC300 control unit of the injection moulding machine. Thanks to shared data storage, the CC300 can precisely coordinate the movements of the machine and the robot with each other, thus optimising overall efficiency. On top of this, the robot paths are especially short due to the tie-bar-less clamping unit of the e-victory machine. Both of these factors contribute to the short cycle times of six seconds in this application.
Compact integration: The pipe distributor by ENGEL fits inside the machine's safety guard.
So that the machine can also be flexibly used for other products, Engel designed the pipe distributor and the bag-packing carts as fixed units. These can be easily moved back and forth, ensuring full accessibility of the mould area. In contrast to many other systems in the market, all components in contact with the product in Engel's pipe distributor are made of stainless steel. This helps to ensure low particle load in the cleanroom.