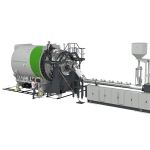
Giant pipes with a diameter of 106 inches can be produced with the extrusion lines recently sold to north-east Africa. With its foray into the new dimension of 106 inches large PE pipes, the extrusion line manufacturer battenfeld-cincinnati has set a new record. These are the first complete lines capable of producing pipes of this and quality. The design incorporates both the company's unique overall system expertise, which intelligently combines the individual components from the material dosing system to the cutting unit without interface problems, and its decades of experience in the construction of large-diameter pipe systems. Continuous optimization to reduce sagging and thus increase pipe quality speaks for itself, as do mechanical engineering aspects that simplify the transport and assembly of the large components.
With the new lines, the two customers will expand their product range to include large pipes with an enormous diameter of 106 inches and thus meet the increasing demand for high-performance fresh water and wastewater systems. Plastic pipes play a major role here, as they are easier to install due to their lower weight compared to concrete pipes, are resistant to corrosion and chemicals and cannot be damaged by tree roots in the ground. In other words, they are functional and durable.
In order to be able to produce pipes in these dimensions, high-performance extruders that can homogeneously plasticize the melt material are required. For some years now, battenfeld-cincinnati has been relying on the solEX NG series, which achieves up to 25 % higher output compared to previous versions. Thanks to the process engineering design with an internally grooved barrel and matching screw and grooved bushing geometry, the extruders operate with a reduced axial pressure profile, which ensures low wear. At the same time, high specific output rates at low screw speeds and temperatures reduced by around 10 °C guarantee effective but gentle melt processing. The OptiMelt static mixer, which is installed between the extruder and the die, achieves a further 10 °C reduction in temperature. The tool itself is a helix pipe head, which, with its two-stage concept, ensures optimum melt distribution with low pressure build-up. Finally, the effective internal pipe cooling supports the stable outlet of the melt from the die. The entire unit thus ensures minimized sagging effects, which is particularly important for large pipes and their logically high weight in order to guarantee optimum wall thickness distribution without ovality.
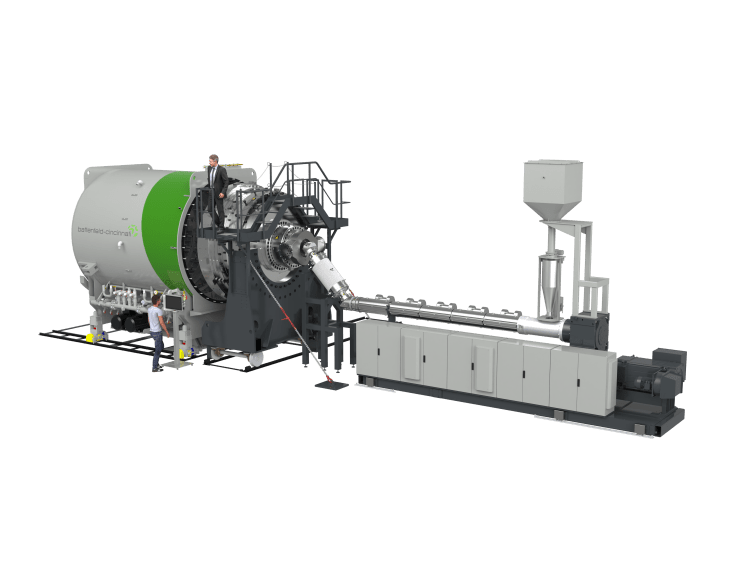
Needless to say, that the downstream components are also designed for the large dimensions and also meet the requirements for low energy consumption. The vacuum and spray baths work solely with frequency-controlled vacuum pumps, which consume around 50 % less energy than conventional systems. At the same time, a closed water circuit in the complete calibration system ensures minimized water consumption of just 4.41 gpm.
A brand new feature is that all downstream components are now only 4m long, meaning that they can be easily transported to their destination and only need to be joined together.
At the booth W3161, the team of experts will be providing information about the specific advantages of large-diameter pipe systems and, if requested, will be presenting the Fast Dimension Change (FDC) system, which can be integrated into any pipe line and allows the pipe dimension to be changed automatically during ongoing operation. FDC systems give the pipe manufacturer maximum flexibility and therefore cost-effectiveness.