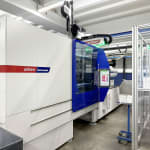
Ein neues Verpackungskonzept in Dünnwandtechnik brachte für die Heinrich Axmann GmbH & Co. KG in Köln die Energiewende beim Spritzgießen. Für dieses Projekt wurde erstmalig in eine vollelektrische Spritzgießmaschine investiert. Die Energieeinsparung liegt gegenüber der Hybridmaschine bei über 30 Prozent. Spritzgießpartner Wittmann lieferte die EcoPower Xpress Maschine mit einem Hochleistungsroboter vom Typ Sonic als vollständig integrierte Gesamtlösung.
Fast jeder kennt das: Beim Öffnen der Verpackung sieht das Fertiggericht köstlich aus. Fleisch und Beilagen sind schön angerichtet. Doch nun kommt der kniffelige Teil: Der Transfer auf einen Teller. Viele greifen zum Löffel, andere stürzen gar den Inhalt der Schale und schon leidet der Anblick und damit allzu oft der Appetit. Heiner Axmann, Geschäftsführer der Heinrich Axmann GmbH & Co. KG, hatte die zündende Idee gegen dieses Dilemma. Er entwickelte eine Kunststoffschale, die sich mit Hilfe eines Aufreißmechanismus‘ entlang des Verpackungsbodens öffnen lässt. Der Verpackungsrand klappt nach oben weg, die Mahlzeit gleitet bequem auf den Teller und sieht dort genauso appetitlich aus wie direkt nach dem Zubereiten und Befüllen der Verpackungsschale. - Unser Kunde hatte Einrichtungen wie Krankenhäuser, Seniorenheime oder Kindertagesstätten im Blick, die keine eigene Küche haben“, berichtet Heiner Axmann bei unserem Besuch am Firmensitz im Stadtteil Rodenkirchen im Kölner Süden. - Jeder soll mit Genuss essen können. Noch dazu unterstützt das neue Konzept höchste Hygienestandards. Die Krankenschwester, die das Essen zubereitet, kommt mit den Speisen nicht in Berührung.

Aus Erfahrung kreativ
Gegründet 1932 und seither durchgehend in Familienbesitz, ist Heinrich Axmann spezialisiert auf die Entwicklung und Herstellung von Verpackungslösungen aus Kunststoff. Schalen und Kännchen für sowohl flüssige als auch feste Lebensmittel, wie Feinkostsalate oder Kaffeesahne, machen einen Großteil des Produktionsvolumens aus. Der umfangreiche Erfahrungsschatz führt immer wieder zu neuen kreativen Lösungen. So kam der Impuls zur Entwicklung der neuen, am Boden zu öffnenden Fertigkostschale von einem Feinkostdeckel, der bereits im Jahr 1979 entwickelt wurde. Die Originalreißbrettzeichnung liegt im Büro von Heiner Axmann noch heute im Schrank.
Mit der jüngsten Neuentwicklung ist dem Unternehmen ein Coup gelungen. - Unser Kunde ist noch im Start-up, hat aber bereits einen Großauftrag aus den USA in Aussicht. Die ersten Schalen im neuen Verpackungsdesign werden in einem Krankenhaus in New York zum Einsatz kommen - Der Kunde ist ein großes Cateringunternehmen, für den in Köln bereits eine große Stückzahl Schalen nach FDA-Standard produziert wurde.

Das Serienwerkzeug ist avisiert. Die Spritzgießzelle dafür steht schon bereit. Gezielt für dieses neue Produkt investierte Heiner Axmann in eine vollelektrische Spritzgießmaschine vom Typ EcoPower Xpress 300 mit 300 Tonnen Schließkraft und einen Hochgeschwindigkeitsroboter vom Typ Sonic. Spritzgießpartner Wittmann lieferte die Produktionszelle als vollständig integrierte Gesamtlösung.
Höchste Einspritzleistung bei stark variierenden Wanddicken
Mit der Fertigkostverpackung schlägt das Unternehmen Axmann auch in Sachen Spritzgießtechnik ein neues Kapitel auf. Die EcoPower Xpress ist die erste vollelektrische Spritzgießmaschine im Maschinenpark. - Lange Zeit war es nicht möglich, Dünnwandverpackungen im Hochleistungsspritzguss auf einer vollelektrischen Spritzgießmaschine zu produzieren - erklärt Heiner Axmann. - Die EcoPower Xpress ist diesen Anforderungen aber gewachsen - Besonders hoch sind die Anforderungen an die Einspritzleistung.
Um die Verpackung aufzureißen, besitzt die Schale an einer der Längsseiten zwei Laschen – zwei, weil bereits bei der Bauteilentwicklung an Linkshänder gedacht wurde. Ausgehend von diesen Laschen führen entlang des Verpackungsbodens im Abstand von etwa 5 Millimetern zwei feine, extrem dünnwandige Linien. Sollbruchstellen, die eine Art Aufreißfaden formen.
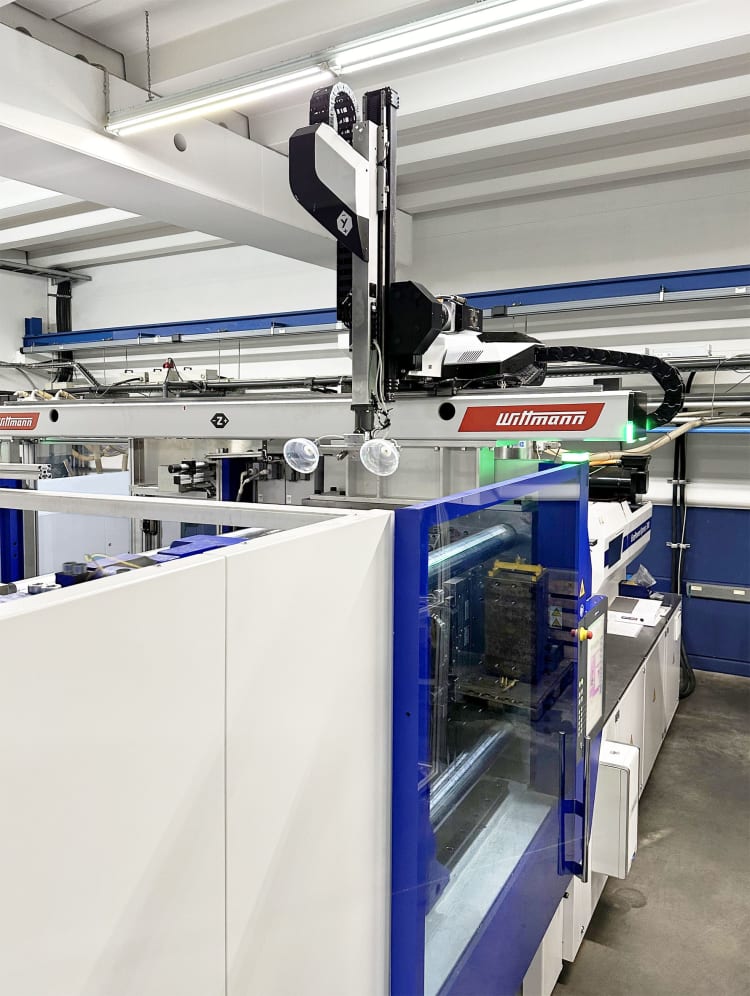
An diesen Sollbruchstellen beträgt die Wanddicke gerade einmal 0,05 Millimeter. Das ist nur ein Zehntel der Wanddicke des Bodens und der Randbereiche. Dennoch muss die Schale, die aus einem PP-Copolymer besteht, beim Einfüllen der heißen Mahlzeit stabil und dicht bleiben. 120 °C ist die Vorgabe. Angespritzt wird zentral am Verpackungsboden. - Unsere größte Herausforderung besteht darin, dass wir beim Einspritzen mit der Schmelze zwei Mal durch diese extrem dünnen Bereiche hindurch müssen, um die Kavität bis in die Randbereiche vollständig zu füllen“, verdeutlicht Betriebsleiter Andreas Brüggemann. - Hierfür brauchen wir eine sehr hohe Einspritzleitung bei äußerst kurzen Füllzeiten.
- Die EcoPower Xpress ist hierfür prädestiniert - sagt Andreas Hollweg, Leiter Vertrieb Spritzgießtechnik von Wittmann in Deutschland.- Die Spritzaggregate dieser Maschinenbaureihe sind für die hier benötigten hochdynamischen Einspritzgeschwindigkeiten ausgelegt - Ein weiterer Vorteil, der vor allem bei der Herstellung von Lebensmittelverpackungen zum Tragen kommt, ist der serienmäßig gekapselte Kniehebel, der eine sehr saubere Produktion sicherstellt.