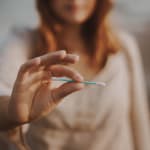
The days of disposable plastic products are numbered – alternatives are needed. The success of LastObject’s reusable cotton swabs shows that the market is ready for change. The company’s basic and beauty cotton swabs are both made of high-quality materials. To meet all requirements, the tip is made of Thermolast M, a compound from Kraiburg TPE that is often used for applications in the health sector.
Every day, 1.5 billion cotton swabs are produced worldwide, each to be used only once. And that’s where LastObject’s mission begins: the Danish company aims to promote the “zero waste” movement to make sure that the next generations will also have a clean and healthy world to grow up in. As the first step, this successful Kickstarter project is supplying reusable, hygienic and reliable alternatives to single-use items we use on a daily basis – with great success, they already sold more than 500,000 LastSwabs to happy customers all over the world. LastObject is thus responding successfully to EU Directive 2019/904, which bans single-use plastic products and will be coming into effect from mid-2021.
The basic requirements for their reusable cotton swab, LastSwab, are durability and quick and easy cleaning. Close attention was given to these qualities during the development process. According to the manufacturer, each individual product is designed for up to 1,000 uses. Another requirement was for the product to be skin safe and not cause any irritation when in repeated contact with the skin. It goes without saying that it meets this standard.
In Denmark, Kraiburg TPE is collaborating closely with Teknisk Agentur, a trusted local distribution partner. The choice of material for the flexible, soft tip was a compound from the Thermolast M series. This compound was also superior to its competitors in relation to processing options, adhesion and look and has the following properties:
- Hardness: approx. 40 Shore A
- Tensile strength: 8.0 MPA
- Elongation at break: 800%
- Tear resistance: 11.5 N/mm
The compound provides adhesion to polypropylene and polyethylene, high abrasion resistance, weldability and freedom from animal ingredients. It is processed using injection molding and extrusion. The rigid stick is made of polypropylene. The case is made of recycled ocean waste plastic (OWP) from the Danish company Zeaplast who collects plastic from the ocean and rivers in southeast Asia and recycles it. The entire product is molded by AMP, a well-known Danish injection molder.
And LastObject is doing more than just following a trend: The product effectively and measurably helps to save raw materials and waste, while reducing the carbon footprint. “It wasn’t only Kraiburg TPE’s material that helped us implement the project. The entire process was very straightforward – all the way from identifying the product through to the service. Kraiburg TPE, Teknisk Agentur, their Danish materials distributor, and the injection molder AMP are reliable partners who are helping us make the future more sustainable,” says Nicolas Aagaard, Co-founder at LastObject.
Thermolast M is available worldwide, US DMF listed and translucent.