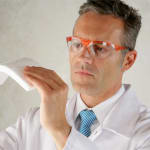
Today, following the successful development of the extruded polystyrene rigid foam panels Styrodur (XPS), the tough-elastic polyolefin range Neopolen, the melamine resin foam Basotect, and the advanced version of EPS for thermal insulation Neopor, BASF has a broad portfolio and unique know-how when it comes to particle and extrusion foams. Continuous research and the launch of new products on the market open up new applications in a lot of industry sectors: the automotive industry as well as aviation, but also solar technology, construction and of course the packaging industry.
BASF has now succeeded with another innovation: E-por, a material which is based on a new formulation and is manufactured in a new production process. E-por is the first tough-elastic, crack-resistant foam which can be transported, stored, processed and recycled like traditional Styropor.
The material is noted for very good fusion of the surface, excellent resistance to solvents, and an appealing look and feel. Because of its high crack-resistance it is multishock-safe and therefore well-suited to being used as transport packaging for high-quality, shock-sensitive electrical and electronic (E/E) products, such as plasma televisions, laptops, refrigerators or washing machines.
Thanks to its special property profile, the new BASF granules offer advantages along the entire value chain for transport packaging – from the converter, the appliance manufacturer and the retailer right to the consumer.
When it comes to the safe transportation of electrical and electronic devices, the weight and sensitivity to shock of the product are crucial. A protective cardboard packaging is usually adequate for transporting robust and lightweight goods.
However, cardboard only absorbs a small amount of energy, so its cushioning effect is limited. This is why cardboard is generally combined with Styropor. Styropor is light and has an excellent cushioning effect. But Styropor is a rigid foam and can break if the packaging is dropped, for example when unloading a truck. Once Styropor has been broken or torn, the cushioning effect diminishes significantly.
As electronic products are becoming lighter and lighter, but electronically more elaborate and thus more sensitive to multiple shocks, the requirements for the packaging are becoming more stringent. This is the reason why valuable and sensitive products are packed in multi-shock safe polyolefin and interpolymer foams.
Compared with the standard packaging material Styropor, these foams have a number of disadvantages in processing and are not as easy to recycle as Styropor.