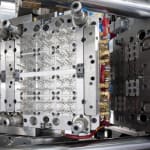
Whether single-component standard moulds, stack moulds or highly
efficient cube and twin-cube systems with in-mould assembly: Foboha builds made-to-measure injection moulds with outstanding technical and economic features. Modular mould concepts and the guaranteed interchangeable design of all mould components provide highest availability at shortest cycle times. At the three locations in Germany, Switzerland and China, in total more than 250 premium moulds are built each year for the packaging industry, medical engineering, personal care and the automobile industry.
Multi-component moulds of Foboha have set the standard for the production of multi-component plastic parts for more than 35 years. Standard technologies like rotary tables, index- and core back processes are used. The biggest built cube mould ever has 192 cavities per parting line and requires a clamping force of 8,000 kN.
Stack moulds provide uncompromising quality and a high degree of efficiency. The competence centre in Muri (Switzerland) builds precision moulds with maximum output which meet the most stringent requirements for producing thin-wall packaging items. Exchangeable mould insert allow the use of base moulds for different products, for example the production of containers with different heights and identical container opening. Innovative cooling technology and selected coatings guarantee the shortest possible cycle times.