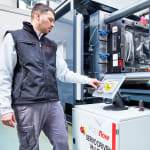
Oerlikon HRSflow has thoroughly revised the software for the control unit of its FLEXflow hot runner systems. The updated Human Machine Interface (HMI) 4.0 now makes operation even more intuitive and convenient. Systems with different nozzle types can be integrated and several parameter sets can be saved per mould. Extended possibilities have been added to individually control each servo motor for nozzle needle positioning and to monitor process stability. In addition, specific user accounts for individual access authorisations can now be set up and managed. Thanks to the web connection, access to the control unit is possible regardless of location.
HMI 4.0 now offers the possibility to control multiple servo motors individually and with specific data. This also enables the handling of systems with mixed nozzle dimensions. For this purpose, the system uses specific mold cards for each tool equipped with the FLEXflow hot runner technology. All the information required by the control system can be uploaded to these cards, including recipes, the number and configuration of servo-electric nozzles. Storing the individual recipes also facilitates changing the working mode of the mould, which is mainly relevant for family tool operations. Even parameters for purging cycles can be integrated. These mould cards can be downloaded on a USB stick to transfer them to another control unit or to save them as a backup.
Advanced process control
To facilitate individual programming and to make it even more intuitive, an image of the respective moulded part can be stored on the corresponding card. There, individual gating points can be correlated to the respective hot runner nozzle. Double-clicking on them allows for disabling or enabling certain functions and checking the status of the motor. Moreover, the user can manage the operation parameters of each motor to independently optimize the performance of the related nozzle. A cycle list page provides master diagrams for individual moulding recipes. Overlaying the appropriate diagram for a specific task with the corresponding actual process data provides the possibility to check the process stability and to take measures where necessary.
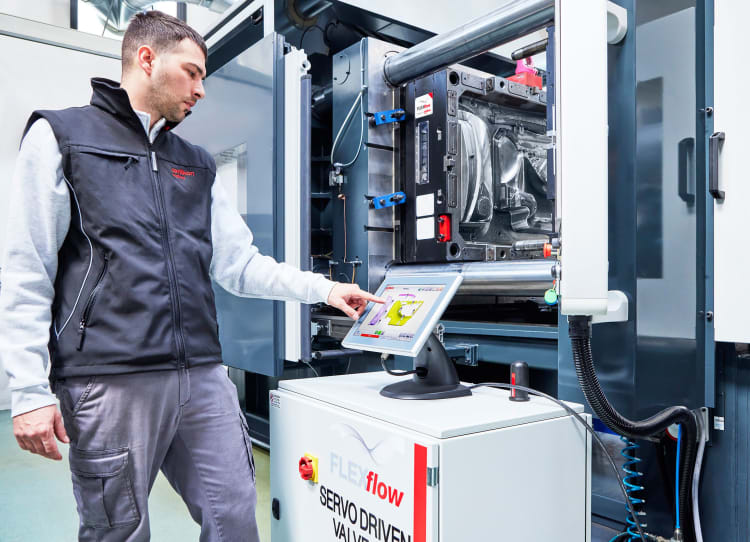
Single and multi-tasking
Creating and storing individual profiles for users or user groups provides customised functionalities which can be flexibly adapted to the respective organisational needs. Each user logs in with his or her personal account name and password. The number of these user accounts is unlimited. Several users can connect to a control unit at the same time. However, only one participant can take control, while the remaining ones only receive information about the respective status. It is possible, however, to pass over control to another user.
Integrated into the customer’s network, the HMI 4.0 allows for controlling FLEXflow hot runner systems from any location via PC or tablet, using an internet browser. The responsive graphic display adapts to the most common monitor resolutions.
Demanding and complex components in focus
Beyond the supplementary advances of the updated HMI 4.0, the advantages of the servo-motor-driven, accurately controllable FLEXflow valve gate systems remain the same. Because large-area moulded parts with high-quality surfaces can be produced, injection moulding of demanding and complex automotive components is one of the main areas of application. Especially in cascade injection moulding, FLEXflow allows individual, sequentially coordinated precise opening and closing of the needles at selectable speeds. This allows the melt flow in the individual hot runner nozzles and the overall volume flow in the cavity to be precisely controlled and the filling process to be optimised over conventional cascade systems. Possible results include not only excellent part surfaces but also a reduction in the required clamping force thanks to the large process window as well as the component weight without compromising quality.