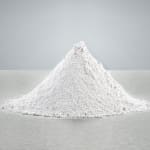
Electrical and electronic applications take on a very important role in our technological and digital everyday life. The demands on electrical performance and mechanical strengths are becoming ever greater. As electronic components become smaller and smaller, entirely new challenges also arise.
In general, the number of E&E applications is steadily increasing with regard to automation and crosslinking in the automotive sector. However, the field of alternative drives holds great potential for heat-dissipating plastics, which are increasingly replacing metals. In many of these applications, the issue of heat generation and its effective dissipation is a major challenge. For example, thermally conductive plastics could be used to improve battery performance. Local overheating during charging and discharging can thus be avoided, while at the same time improving overall thermal management. The effectiveness and service life of the battery are increased. The same applies to the use of thermally conductive plastics in electric vehicle charging stations and power electronics.
Traditional air cooling of electronic components is disappearing due to the ongoing miniaturization of assemblies containing a larger number of components with high energy density. Heat sinks in conjunction with thermally conductive surfaces are often taking their place. Air, with its low thermal conductivity, can significantly impair heat transfer between the heat sink and the component. Innovative gap fillers with the thermally conductive Silatherm products can make an important contribution here.
In electronics, potting is a process of filling a complete electronic assembly with a solid or gelatinous mass to resist shock and vibration and to exclude water, moisture or corrosive substances. Thermally conductive electrical potting compounds are an attractive option for temperature reduction and performance enhancement in e-mobility. In addition to chemical and moisture resistance, high heat dissipation and excellent electrical insulation are required. The Silatherm product range significantly increases the thermal conductivity as well as the mechanical properties of plastics. At the same time, the materials meet the requirement for insulation against electric current.
High-quality electrical components thanks to Silbond fused silica
In addition, electrical potting compounds in combination with metals can be subjected to severe thermal alternating stresses, a common cause of component damage. The outstanding property of fused silica is an extremely low coefficient of thermal expansion combined with excellent electrical insulation. The use of Silbond fused silica enables the production of high-quality, complex components from different materials and prevents cracking.
High-performance fillers for better performance
As you can see, mineral fillers have long since ceased to be inexpensive "gap fillers"! They can be used to specifically modify the properties of modern polymer systems and adapt them to special requirements. Innovative acicular and platelet-shaped functional fillers, such as wollastonite, mica and kaolin, give thermoplastics, thermosets and elastomers outstanding mechanical strength and thermal properties. For all products, significantly improved homogenization can be achieved by a surface coating tailored to the customer's system. This leads to even better mechanical and thermal properties.
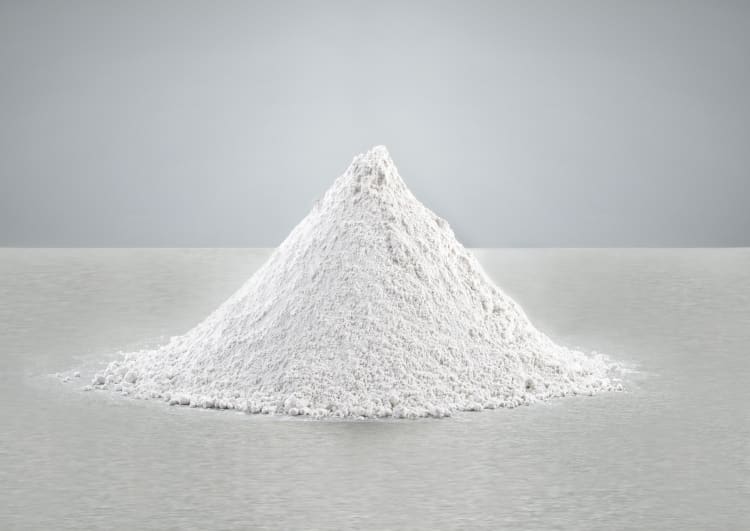
Company Profile
about Quarzwerke Group
The Quarzwerke Group is an independent international family business with more than 140 years of tradition and a significant market position in the extraction, processing and refining of industrial minerals, mainly from its own deposits. More than 35 production sites have been located in Europe for a long time.
Headquartered in the vicinity of Cologne, Germany, the company is organised into six divisions. Approximately 3,500 employees in the Quarzwerke Group work on contributing to the success of our customers worldwide.
The company always combines high-quality mineral raw materials with modern and efficient processing technologies. The high quality of service, which focuses on the importance of customer satisfaction, exceeds expectations. The whole Quarzwerke Group sees itself as an efficient and reliable partner with social and ecological responsibility.
about division HPF The Mineral Engineers
The division HPF The Mineral Engineers has been developing and selling innovative high-performance fillers and additives for polymer systems based on natural and synthetic minerals for years. Thanks to the long lasting experience and equipment HPF is in a position to help customers around the world to improve their polymer systems by unique filler solution in the sectors:
- Thermoplastics
- Thermosets
- Elastomers & Rubber
- Adhesives
- Construction Chemicals
- Paints & Coatings
A whole team of highly trained specialists is employed in the research and development as well as in the laboratory. In 2021, HPF Minerals Tech Ltd. state-of-the art production plant went into operation in Dangjin, South Korea additionally to HPF site in Frechen, Germany. Both production sites with its experienced personnel, can adjust flexibly and quickly to new problems and products. Units of various s are available in our plants for the processing and surface treatment of mineral raw materials ranging down to a few hundred nanometers. The high-performance fillers produced in proven quality are supplied all over the world.
about KiZPPS Osiecznica
KiZPPS Osiecznica is also part of Quarzwerke Group. The plants of KiZPPS “Osiecznica” and TKSM “Biała Góra” produce quartz sands for the production of glass and ceramics and for use in foundry, construction chemicals and other industries. Moreover, the KSM “Surmin Kaolin” plant produces kaolins which are mainly used in ceramics, rubber and plastics. With a focus on polymer applications and composite products, the technical sales department in Poland is open to any question related to the use of functional fillers and will certainly find the individual customized solution.