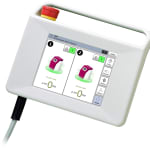
As part of its constant pursuit of sustainability and economical use of resources, Wittmann Battenfeld has been offering its customers for many years expert knowledge in application technology as well as equipment developed and manufactured in-house for Airmould internal gas pressure technology and Cellmould structured foam technology. With the recently completed further development of Airmould, the company has now created an even more compact and more user-friendly system, which offers users a number of additional advantages.
Airmould internal gas pressure injection molding is a process in which nitrogen is injected into a mold cavity already partly or completely filled with plastic melt, thus forming an internal cavity structure. In this way, light-weight parts can be produced within a short cycle time and with good surface attributes as well.
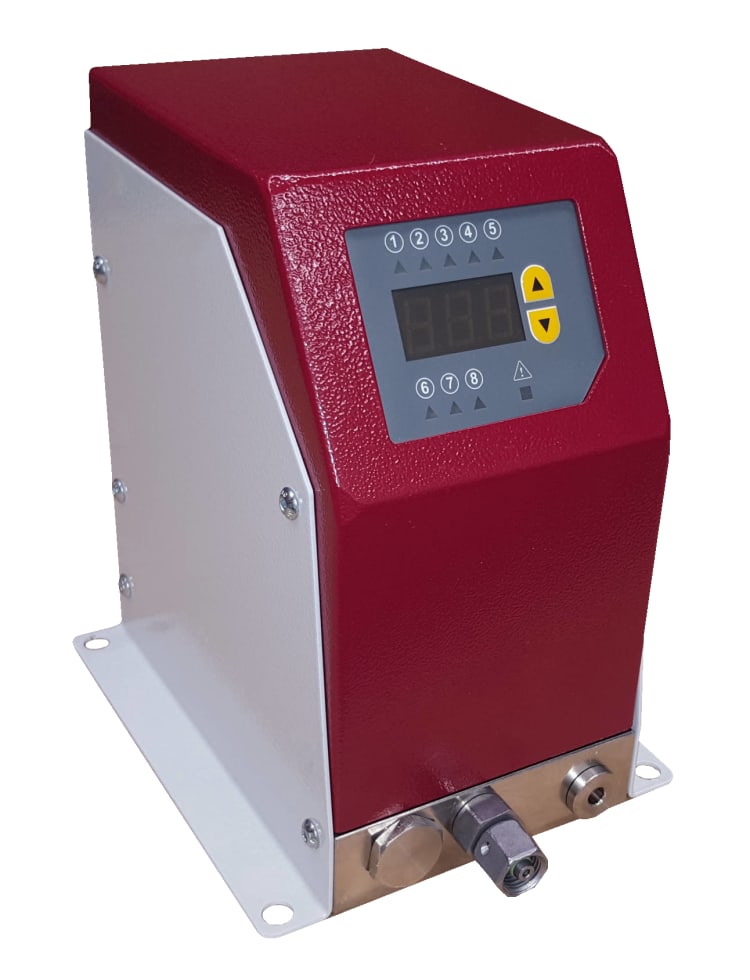
All the necessary components for this process have been developed by Wittmann Battenfeld. The Airmould package includes a nitrogen generator unit, which extracts the nitrogen directly from the surrounding atmosphere, so that no costs for nitrogen supplies are incurred by users. The compressor unit, also developed and manufactured in-house, is able to compress the nitrogen up to a maximum pressure of 330 bar. Both these units can be combined into a single appliance and thus supply several injection molding machines with nitrogen via a system of hose connections. On Wittmann Battenfeld machines, the pressure control module installed on the mold or on the machine’s clamping plate can be set directly via the machine’s control system. If Airmould is used on machines of other brands, an additional manual operating device is required. A control cabinet was previously necessary for operating more than two modules.
For Airmould Next, the next generation of internal gas pressure technology, Wittmann Battenfeld has thoroughly re-designed both the pressure control module and the manual operating device. The main focus of this work lay on even more user friendliness, better quality monitoring and compact design.
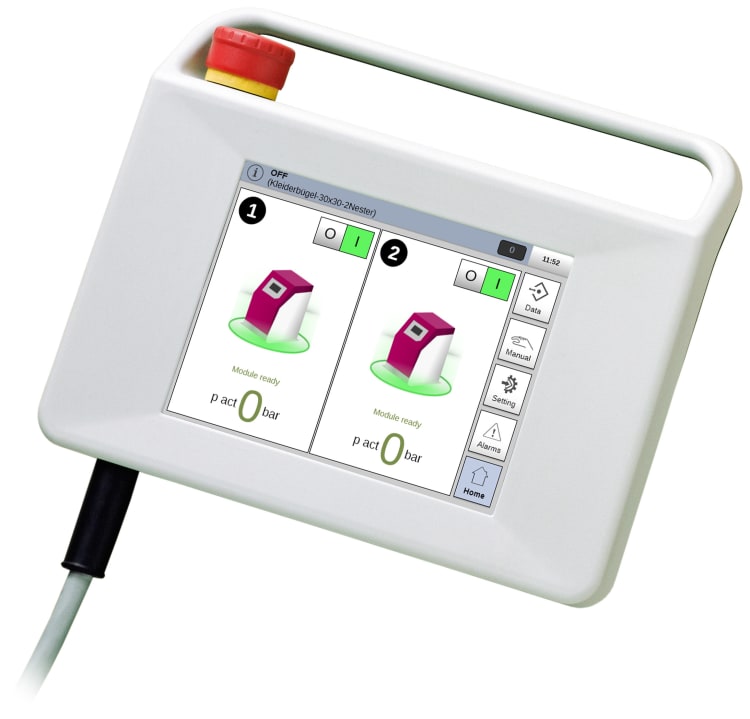
The pressure control module, previously available in two different versions (a mono module controllable via a hand-held device, and a standard module controllable via an external control cabinet), have both been replaced by one uniform system. Top priorities in creating the new module were compactness and optimized design. For example, the new module is about 15% smaller than its predecessor. Moreover, the monitoring function of this appliance has been improved considerably.
The new manual operating device scores above all by its high user friendliness. With this small, compact appliance, up to 8 pressure control modules can be operated without the external control cabinet required by the previous technology.
So the advantages of the new Airmould Next system are obvious:
- The system stands out by its space-saving design and is thus ideally suited for production halls with little free space. The components can be integrated flexibly into the injection molding machine. An external control cabinet is no longer required.
- The reduction to a uniform system enables more flexible use of the technology.
- The easier operation saves time and consequently costs.
- Significantly lower investment costs than previously incurred thanks to harmonization and compactness of the new system
- Better quality through improved monitoring function
Airmould Next can be demonstrated directly on site in the technical lab at Wittmann Battenfeld Germany in Meinerzhagen or digitally via Wittmann Interactive – currently on a servo-hydraulic SmartPower 120/525.