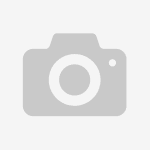
Akulon Ultraflow PA6 from DSM Engineering Plastics is characterized by excellent material properties in combination with optimized processability. Above all, the polymer offers superior, up to 80 % higher flow rates than conventional nylon resins, and can thus be molded more easily.
As a result, the improved injection performance leads to cycle time reductions of up to 40 %, depending on the specific application. In addition, the material can be processed at lower temperatures, contributing to enhanced energy efficiency. Higher injection speed and faster crystallization allow molders to operate with lower clamp forces (smaller machines) or higher-cavity molds. This in turn reduces the cost per part or also the machine hour rates.
Altogether, these benefits provide molders with a high cost savings potential - a whole bundle of bottom line results that also convinced German rail car model maker Modelleisenbahn Schirmer from Borna near Leipzig. The bogie of a Deutsche Reichsbahn gondola car demonstrates the high demands in precision and detail to be met by these models from the Ore Mountains in southern East Germany.
In the past, job molder Auhagen GmbH, based in Marienberg near Chemnitz, had molded bogies for a Schirmer gondola car model in acrylonitrile butadiene resin (ABS). The parts showed sink marks and warpage, and the ABS gave the surfaces an undesirable glossy finish. Full-scale car bogies have surfaces matted from abrasion and weathering. For these reasons, Auhagen und Schirmer in collaboration with Ter Hell Plastic GmbH searched for an alternative that would permit greater attention to detail.
As ideal solution for this gondola car model application, Akulon Ultraflow from DSM did not only meet the requirements for greater detail, but also helped to improve the processing conditions, exhibiting its superior flow properties in the precision injection molding of train car models.
This permits small-scale reproductions to the finest detail and a lot more faithful to the original - an important requirement especially in the TT scale (1:120), where detailing is more difficult than in the H0 scale (1:87.5).
Furthermore, Akulon Ultraflow was also instrumental in optimizing the cycle time of the application, a key parameter for the responsible production managers. Customer Schirmer was particularly satisfied by the favorable material properties. The bogies have become inherently more rigid, and the former gloss is gone. Better resilience and great looks - side effects that play more than just secondary roles in model making.
DSM Engineering Plastics is a Business Group in the performance materials cluster of DSM, with sales in 2007 of EUR 839 million and approximately 1550 employees worldwide. It is one of the world's leading suppliers of engineering thermoplastics offering a broad portfolio of high performance products including Stanyl high performance polyamide and Akulon 6 and 66 polyamides, Arnitel TPC, Arnite PBT and PET polyesters, Xantar polycarbonate, Yparex extrudable adhesive resins.
These materials are used in technical components for electrical appliances, electronic equipment and cars, in barrier packaging films as well as in many mechanical and extrusion applications. With Stanyl, it is the global market leader in high heat polyamides.