Automated coil changes made easy - The new coil change module sets new standards
Like its big brother, the ProfilControl 7 system, Allroundia DV now also comes with an integrated section tracking feature that automatically generates a defect or batch report for every batch produced.
This is enabled by linking AllRounDia via generally available interfaces such as OPC-UA or classical direct IO wiring with the main line. In this way, the system can communicate with the cutter or the coiler. If the product is recoiled after the cutter or there is a coil change, AllRounDia receives a corresponding signal. The defects identified during the continuous extrusion process are assigned to the current coil in process and the defect positions calculated relative to the head end of the coiled product. When the product is downcoiled for subsequent processing, it is thus possible to exactly locate the defects and remove the defective material from the production process. This saves both time and costs.
Moreover, the AllRounDia system now provides numerous further networking options that to date have been reserved to the bigger ProfilControl systems.
Dependable defect recognition at any speed - No problem for an encoder
AllRounDia DV is now available with an encoder, making the system even better suited for use with varying extrusion line speeds. While the basic version makes the defect calculations on the basis of a fixed time sequence, the encoder makes use of the line speed to calculate the exact defect . By ensuring that the resolution at which the defects are recorded is always adequate and constant, the encoder makes defect detection even more accurate and dependable.
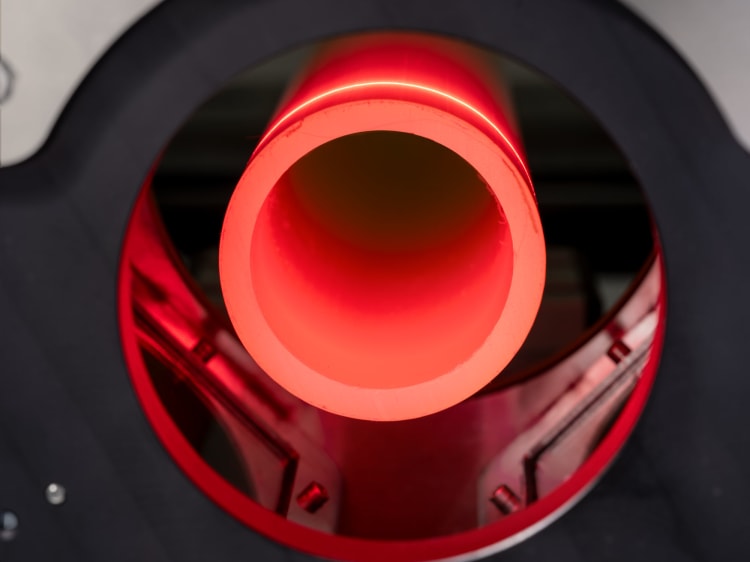
Keeping track of operator settings The new Scada Log module makes it possible
Have the parameter settings been changed or has the threshold for the defect been raised or lowered? The Scada Log module stores and documents any interactions between the operators and the inspection system. In this way, it is possible to track alterations quickly and reliably and clearly relate them to the respective operator.
AllRounDia DV - or, in other words: Truly reliable 2-in-1 inspection for all round-product applications
AllRounDia DV inspects the surfaces and diameters/ovality of hoses and tubes 100 percent, continuously and around the entire circumference. It can also handle glossy surfaces as well as translucent and semi-transparent hoses. The measurement of the diameter can be separately switched on and off, as required. As a two-in-one solution, AllRounDia DV is the perfect choice for both newly installed lines and as a replacement in existing lines - in any case, a truly cost-cutting dual-purpose system.
With the software upgrade, AllRoundia DV has become a member of the ProfilControl 7 product family, offering a comprehensive range of attractive system extensions. Whether in order to be integrated into the Manufacturing Execution System (MES) of the production line or to further enhance defect evaluation and analysis performance: AllRounDia DV can now be extended with virtually every module that its big brother uses.
Practice-proven: Successfully tested at Becker Plastics
At Becker Plastics in Datteln, Germany, the extrusion is the beating heart of the production. A member of Roth Industries, the company produces plastic and composite pipes for heating and plumbing systems and for numerous other applications and industries. The quality requirements are very high, knows Pierre Baranowski, Head of Operations at Becker Plastics. Flaws are not tolerated. After successful pilot tests, which have confirmed the performance capabilities of the new AllRounDia DV from Pixargus, Baranowski is very much in favour of using this innovative solution for quality control in its production processes. “It is vital for us to recognize defects and the sources of defects early on in the production process and be able to take immediate remedial action. Here, the inspection system from Pixargus provides us the best possible support,” says Baranowski.“