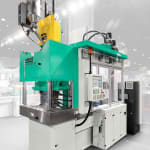
From 5 to 7 February, Arburg will present two sophisticated injection molding applications at Plastec West 2019 in Anaheim/CA, USA: At stand 4001 in hall B, a turnkey system built around a vertical Allrounder 375 V will produce radius gages in fully automatic production. The second exhibit, an electric Allrounder 370 A in clean room version, will be shown with a medical application.
"With our headquarters in Rocky Hill and the two Technology Centers - Midwest and California - we have a strong presence in the USA," emphasizes Friedrich Kanz, Managing Director of Arburg Inc. "Our team of experienced application technology specialists, project and service engineers uses its extensive know-how to create sophisticated turnkey systems in close cooperation with customers. In Anaheim, we will show a 'Made in USA' production cell with a unique space-saving design, used to overmold metal inserts to produce radius gages, as well as a machine in clean room version for medical applications."
Automated overmolding of inserts
Arburg offers a wide range of automation solutions from a single source. These solutions cover everything from simple pickers to six-axis robots and complex turnkey systems. At Plastec West 2019, the company will present a production cell developed by Arburg's automation experts in the USA.
A vertical Allrounder 375 V with 500 kN (55 tons) clamping force and a size 170 (3.7 oz) injection unit will be used for the automated production of radius gages. The required handling tasks will be performed by a Multilift Select linear robot system positioned on the machine to save space. On In two mold cavities, the metal inserts will be overmolded with 30 percent fiberglass-reinforced PA 6.6 using two different methods - in a cycle time of around just 45 seconds. For the first version, the robot system first subjects the metal components to a plasma pretreatment and inserts them into the first mold cavity, where the plastic is molded onto the plasma-pretreated surface. In the second version, an untreated insert is placed into the second mold cavity and the plastic is molded onto the metal component on both sides, creating a mechanical connection. Finally, the finished parts are removed from the two-cavity mold and placed in a part exit chute.Allrounder for medical applications
In addition to the standard range, Arburg offers special clean room solutions. The modular product range enables Allrounder injection molding machines and production cells to be very precisely tailored to customer requirements and the application at hand.
At Plastec West 2019 an electric Allrounder 370 A of the high-performance Alldrive series in clean room version will be showcased that produces lever bolsters (medical components for minimally invasive surgery). A clean-air module with air ionization above the clamping unit provides for low-particle air in the working area. It allows to develop a clean room environment inside the clamp area. Thanks to ionization and HEPA filters, the clean room module ensures a high level of air circulation and neutralizes electrically charged molded parts. The machine can be docked to a clean room via a conveyor belt.The electric Allrounder machines from the Alldrive series are characterized by speed, precision and energy efficiency. The main axes for injection, dosing, and opening and closing the mold are servo-electrically driven. High acceleration and final speeds combined with simultaneous machine movements result in greater cost efficiency by reducing the cycle time. The closed servo electric drives are liquid-cooled, direct driven, operate quietly, and prevent exposure to dust caused by abrasion.