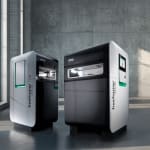
TCT Asia, held from 21 to 23 February 2019 in Shanghai, China, is Asia's largest exhibition for additive manufacturing (AM). At stand D60 in hall W5, Arburg will use the opportunity to showcase additive production of functional plastic components made from qualified original materials.
Two 200-3X freeformers will process medical TPE-S and flame-proof PC for applications in the medical technology and electronics industries. Several dozen components will also serve as examples to demonstrate the capabilities of Arburg Plastic Freeforming (APF).
"The market for additive manufacturing is growing rapidly and offers an interesting production technology solution to complement injection moulding," says Lukas Pawelczyk, responsible for global freeformer sales at Arburg. "With our decades of know-how in plastics processing and our two freeformers in sizes 200-3X and 300-3X, we offer attractive solutions for both experts and newcomers to additive production using the APF process."
Original materials for medical and electronic components
The APF process is ideally suited to the industrial additive manufacturing of functional components. This includes individual plastic parts for consumer goods, spare parts made of original materials and implants for medical technology. FDA-approved TPE-S (Medalist MD 12130H) with Shore A hardness 32 can only be processed on the freeformer. The machine at TCT Asia 2019 will use the material to produce soft medical components with the aid of a support material. The second 200-3X freeformer will process aerospace-approved PC with flame-proof properties (Lexan 940) for applications in the electronics industry.
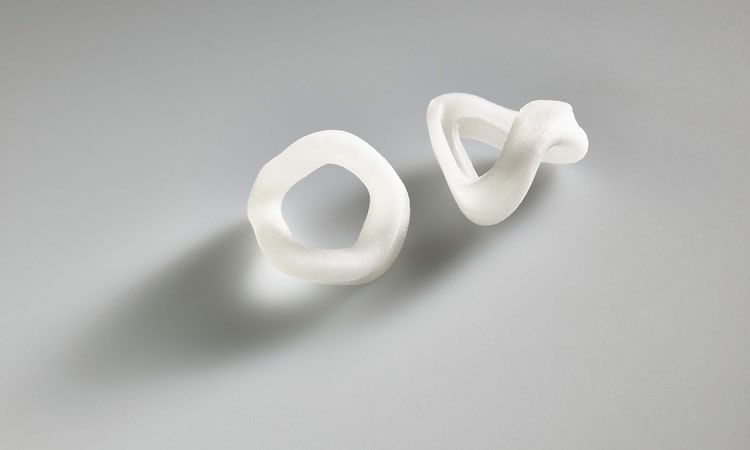
A wide range for industrial additive manufacturing
With the 200-3X freeformer, featuring two discharge units, Arburg already covers a wide spectrum for industrial additive manufacturing. The new 300-3X freeformer is even able to process three components and therefore produce complex functional components in resilient hard/soft combinations with support structures. This is unique to date within the industry. The pair of freeformers will demonstrate the production of the desired plastic parts in reproducible high part quality. They can also be connected to an MES, such as the Arburg ALS host computer system, and be automated with robotic systems. This enables integration into IT-networked production lines. If necessary, the relevant process and quality parameters can be traced back to the specific part.
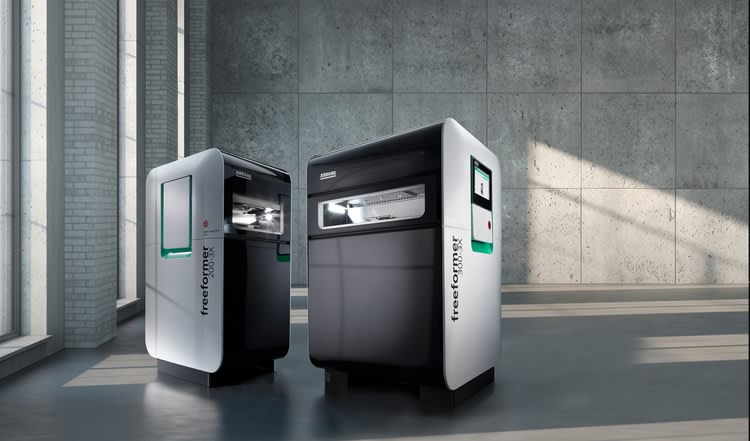
With the 300-3X freeformer, the designation 300 stands for the available part carrier surface area in square centimetres. It is almost 50 percent larger than that of the 200-3X freeformer. "3X" refers to the three axes of the part carrier movable in the x, y and z directions. The build chamber now offers space for larger small-volume batches and 50 percent wider parts with dimensions of up to 234 x 134 x 230 millimetres.
Numerous components and interactive stations
Trade visitors to TCT Asia 2019 can also gain an impression of the capabilities of the freeformer exhibits based on numerous functional parts. Exhibited parts will include gripper fingers in hard/soft combinations, cable clips made from PP, transparent test discs made from PMMA and bellows made from elastic TPE.
Two interactive stations will be available where trade visitors can test the functionality and durability of selected functional parts for themselves. These will include a very thin and elastic "spider membrane" made of medical TPE-S, screw caps made of PP and skull implants made of resorbable PLLA.
Benchmark parts for potential customers
In the Arburg Prototyping Center (APC) at the German headquarters in Lossburg, a number of freeformers produce benchmark parts for prospective customers. Further machines are used for the same purpose at the company's subsidiaries across the world, including in Asia. Before any customer purchase, preliminary trials are conducted to determine whether the technology is actually suitable for the desired part, material and application.
Source: Arburg