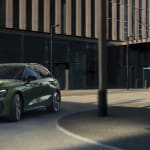
For the first time, Audi is mass-producing painted radiator grilles made from a blend of polycarbonate (PC) and polyethylene terephthalate (PET) recyclates for the new Audi A3 Sportback and Audi A3 Sedan. This groundbreaking achievement is the result of a collaboration between Mocom, a specialist in compounding and recycling, Winning Plastics, a leading plastics processor, and Audi.
“Our objective is to systematically increase the use of recycled materials in Audi vehicles. With the A3 model update, the painted radiator grille ontains a significant portion of secondary raw materials for the first time. As a key design element of Audi models, the grille must meet high standards in design, appearance, and quality, in addition to specific mechanical requirements,” explains Frank Fischer from Audi’s Materials Engineering department.
The project team encountered challenges due to the stringent technical requirements for mechanical properties in safety-critical components and the high purity needed for the material to be reused in painted parts. “Developing and producing radiator grilles with recycled content was an exciting process”, says Werner Meschitz, Head of Innovations at Winning Plastics. “Suitable recyclates were not available off-the-shelf, so together with our partner Mocom, we developed a recycled compound that partially incorporates painted scrap components from our own production. Standard recycling methods for scrap parts leave too many contaminants and paint residues, making it impossible to reuse the material in a new radiator grille. However, Mocom’s innovative process, particularly in paint removal, ensures the required purity of the recyclate, enabling a closed-loop recycling system.”
How does paint removal from plastic parts work?
The recycling process begins with scrap parts from production, known as post-industrial materials. In this case, these are painted radiator grilles with purely cosmetic defects, such as dust inclusions. After the defective parts are shredded into approximately 30-millimeter pieces, they are processed in a hammer mill uniquely designed by Mocom. Here, the paint is removed primarily through friction, and the resulting debris is vacuumed away. The paint residue is discarded, while the de-painted PC+PET material is further processed into regranulate.
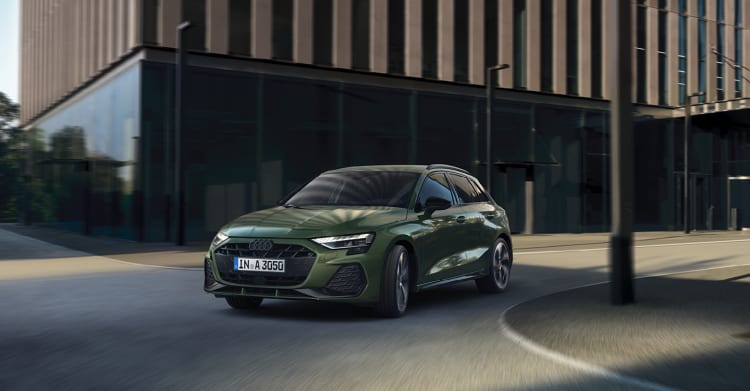
Next, during extrusion, the plastic mass undergoes fine melt filtration, where it is passed through special filters. The resulting PC+PET recyclate is then blended at a nominal 27 percent into the production of new radiator grilles for vehicle manufacturing. This process offers a cost-effective recycling solution with a lower carbon footprint compared to using new materials.
“As experts in processing production waste, contributing to the development and implementation of this sustainable solution was an exciting challenge for us at Mocom,” says Thomas Marquardt, Managing Director of Sales, Marketing & Development at Wipag, a Mocom subsidiary. “Our unique technologies enabled us to create a high-quality plastic compound with recycled content that meets the stringent requirements for manufacturing radiator grilles. The successful integration of recyclates in automotive plastic components opens up new opportunities for the entire automotive industry."