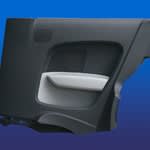
Use of the new grade has enabled the auto maker to produce an interior part with exceptional surface aesthetics and soft-touch qualities, without the need for typically required painting.
Interior applications in premium-class models have been dominated by other polymer solutions such as PC/ABS (polycarbonate/acrynitril butadiene styrene) with soft-touch painting. “By achieving a surface quality superior to traditional materials without using paint, the Softell PP compound used in the Audi A1 interior door panel has established new aesthetic and resource-efficiency benchmarks in premium-class models,” said Erik Licht, LyondellBasell’s global marketing manager for the Volkswagen group. Finished parts made out of Softell resins offer improved recycling potential due to the elimination of the coating step.
The gloss level of a conventional PP compound is between 2 and 3 GUs (measured at an angle of 60°). Tests conducted using a gloss meter show that Softell resins have a gloss level below 1.5, which is required to achieve good matt surface characteristics. To attain this level of gloss, the use of soft-painted surfaces typically has been required. “The low level of gloss achieved with the use of Softell resins enables Audi to produce a door panel with the desired low light reflection. They have achieved their quality and performance requirements without the need for costly painting processes,” said Licht.
Compared to traditional polymers, the grade also provides the automaker with improved flowability in high shear and injection molding conditions. Added Licht: “The improved flowability was essential to produce the model’s highly sophisticated loudspeaker grill that’s integrated into the door panel Audi had very demanding requirements especially on the loudspeaker grill structure and reproducing such a fine surface structure was achievable due to the enhanced flowability of the grade. We’ve been able to achieve these performance characteristics through R&D activities focused on the continuous development of innovations that address growing customer needs for aesthetics, cost-effective production and reduced environmental impact.”