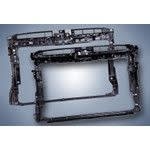
In addition to limited space for installation, the requirements to the all-plastic part include a variety of very challenging load cases: among them, static and dynamic hood latch failure, where incorrect opening and closing of the engine's hood is simulated and tested under the harshest conditions. At the same time, the stiffness and vibration behavior of the system comprising front end and radiator was optimized on the basis of CAE analyses and validated in an actual vibration test.
Special attention was devoted to the crash sensors attached to the front end. They ensure deployment of the airbag at the right moment in the event of a head-on collision. For this, the plastic part must exhibit a certain dynamic stiffness at a defined location and satisfy the automaker's crash acceleration requirements. In a real-world test, the vibration response of the part corresponded exactly to what was designed and predicted by Ultrasim: The Ultramid front end carrier transmits the collision signal correctly.