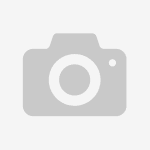
The plant has the capacity to produce 90,000 tpa of Neopor. BASF says the insulating capacity of Neopor is up to 20% better than that of Styropor EPS, and will target the growing need for improved building insulation to combat rising CO2 emissions.
BASF says the advantages of the new extrusion process is that it yields more uniformly sized granules and will permit a targeted setting of the panel properties, for example compression resistance. It added the new plant will ensure greater delivery reliability to its customers and give BASF greater flexibility to quickly respond to shifting market demands.
Dr. Martin Brudermüller, responsible for plastics on BASF’s board of executive directors, said: - Even though the global financial crisis has also had a negative impact on the construction sector, the worldwide demand for energy-efficient products will continue to grow, particularly for retrofitting thermal insulation in old buildings as well as for cooling buildings.
BASF expects the global market for EPS in the construction sector to grow by about 5% per year. In Germany, about 30% of all EPS-based insulating materials are currently used in new buildings, while 70% go into renovation projects. The latter figure is expected to rise to 75% by 2012.