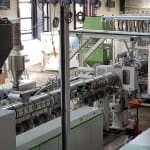
The latest addition to the battenfeld-cincinnati Germany GmbH pilot plant in Bad Oeynhausen is a multifunctional thermoforming sheet line. The complete extrusion line is equipped with cutting-edge machine components and can produce sheets and thin boards made from new materials, recycled materials, bioplastics, and combinations of materials. ''The new pilot plant line will enable our customers to develop new types of sheets or optimize their existing products – something that is becoming increasingly important in the context of ''design for recycling'','' says CTO Dr. Henning Stieglitz. The core components of the pilot plant line are the high-speed extruder 75 T6.1, the STARextruder 120-40, and the Multi-Touch roll stack with a width of 1,400 mm. The three modern units clearly demonstrate that the specialist in sheet and board extrusion is committed to developing and improving its individual components and, hence, its complete extrusion lines on a continual basis and is constantly adapting to changing requirements in the industry. The extrusion line comprises the two main extruders and a 45 mm coextruder, each with a multi-component dispensing unit, melt pump, and screen changer, a feed block for B, AB, BA, or ABA layer structures, as well as the Multi-Touch roll stack with subsequent winder. Depending on the configuration, the line can achieve a maximum output level of 1,900 kg/h for PP or PS and around 1,200 kg/h for PET with line speeds of up to 120 m/min.
When pilot plant tests are carried out, the relevant machine components are combined in line with the product specification. If materials such as PS, PP or PLA are to be processed into sheets, the highspeed extruder is used as the main extruder. The tried-and-tested compact processing machine with a screw diameter of 75 mm and a processing length of 40 D is very energy-efficient and now offers better performance levels than ever before. High-speed extruders ensure optimum melt characteristics and enable rapid product changeovers. The STARextruder, on the other hand, is ideal for producing PET sheets from new or recycled materials. The single-screw extruder with central planetary roll section processes the melt very gently and achieves exceptional degassing and decontamination rates thanks to the large melt surface in the central section. ''The STARextruder really comes into its own when processing recycled materials, as it reliably removes volatile components from the melt. When it comes to the possibilities that this system can offer in the context of the circular economy, there is still a huge amount of untapped potential,'' says Dr. Henning Stieglitz.
The Multi-Touch roll stack ensures outstanding sheet quality regardless of the raw materials used. The special functional principle of this type of roll stack means that the top and bottom of the sheet or board can be cooled almost simultaneously, thus achieving much better transparency and flatness. At the same time, the tolerances can be significantly reduced due to the increased number of effective nips. Reductions of 50% to 75% can be achieved. The two main precalibration rolls are arranged in a 45° position – ideal for PET processing.
Many of the key issues facing the packaging industry at the moment relate to the recyclability of its products. Mono-products with a corresponding properties profile, alternative material combinations, or bioplastics are just some of the options being considered in the context of ''design for recycling''. Dr. Stieglitz: ''We are confident that the new pilot plant line will not only demonstrate our machine expertise in this sector, but will also provide our customers with a special service, enabling them to work together with us to produce and test optimized sheets under production conditions.''
Source: battenfeld-cincinati