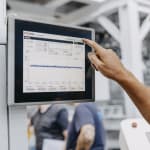
The increased use of recyclates and raw materials from different sources makes it much more challenging to keep extrusion processes under control. The inline viscometer Visco-P from Promix Solutions can help to stabilize and monitor the extrusion process at the same time. But when is the right time to monitor the quality of the product? Before the process, the quality of the raw material can be assessed and approved or blocked by means of random samples. A 100% inspection of finished products is difficult, expensive and ultimately too late, as the defect can often no longer be rectified. This leads to additional costs and possibly to the re-production of an entire series.
During the process, characteristic values such as melt pressure, melt temperature, extruder speed, layer thicknesses and similar parameters are recorded and evaluated as required. However, the actual material properties, which can change due to material composition, additive and color content, temperature, pressure and shear, are not measured and therefore cannot be used for quality assurance.
The inline viscometer Visco-P from Promix-Solutions is helpful for quality in extrusion in two ways. Firstly, the installed measuring module homogenizes the polymer melt and secondly, it measures the actual viscosity of the entire melt under process conditions and in real time.
The Promix measuring modules, which are specially adapted to the process, homogenize the melt including the additives and colors added. Of course, this also applies to mixtures of virgin material, B-goods, recyclates and regranulates. Another side effect is the homogenization of the temperature across the pipe cross-section. All of these effects result in a more uniform end product and can lead to savings in color or additive dosing.
The measuring module also serves as a capillary for online viscosity measurement. The real viscosity is determined using known process parameters such as material type, throughput, melt temperature and the pressure loss across the mixing module and output in real time as a graph and numerical value. In addition to the viscosity, the current melt temperature and the shear rate are displayed graphically. All other important parameters are displayed and saved as numerical values.
The conversion from real viscosity to solution viscosity (IV) for PET is also included, as is the conversion of viscosity to MFR for polyolefins and similar materials. This makes it easier for the user to compare the displayed values with the specifications.
User-selectable upper and lower limits for the viscosity trigger an alarm and show the operator the current deviations from the target value. Subsequent adjustments and their effects on the process and thus the viscosity are displayed directly on the Visco-P and make it easier for the machine operator to take corrective measures to optimize quality.
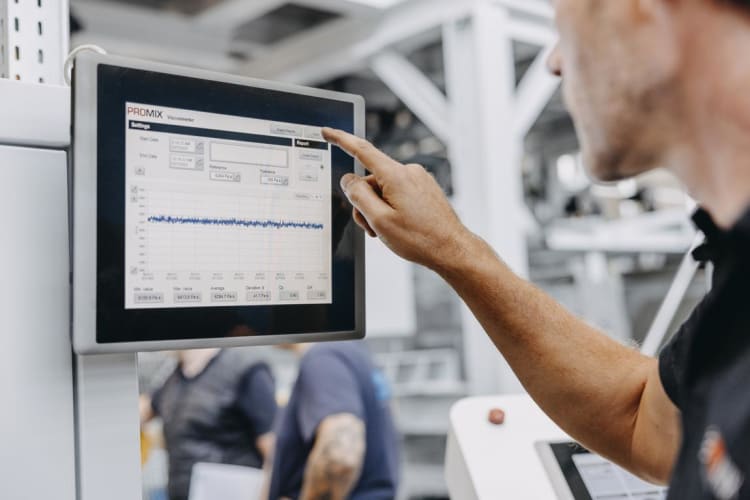
As all relevant data is stored for 12 months, corresponding evaluations can also be read out and assessed after the end of production. There are three ways to do this with the Visco-P. The data can be sent directly to another control unit via an external interface (FieldBus, ProfiNet, etc.) and processed there. The data can be read out via TeamViewer or a USB stick, saved and evaluated by an external computer. The third option is integrated in the Visco-P and creates a report on the viscosity with all relevant framework conditions and statistical evaluation with maximum value, minimum value, average value, deviation, Cp and Cpk. In addition, the viscosity is displayed graphically over the observation period with upper and lower limits. The graph can be adjusted on the X and Y axes according to the user's requirements. The start and end time of the report can also be freely selected by the user. The creation of such a report is particularly convenient using the start-stop function. The machine operator starts recording the values in a report using the start button and ends the recording with the stop button. The Visco-P immediately generates a report for the batch produced. This report can be attached to the batch and thus supplements the quality data of the finished product.
This makes the Visco P an ideal addition to quality control before and after production. The improved mixing of the components with simultaneous monitoring of the viscosity facilitates the processing of recycled material or viscosity-influencing additives such as chain extenders for PET.
The Visco-P is compatible with all common extruder designs and can be retrofitted to existing systems. It can be used for almost all polymers and is very easy to operate.