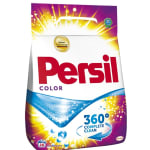
Borealis and Borouge, leading providers of innovative, value-creating plastics solutions; and Henkel, a global market leader in the adhesives sector and owner of leading laundry, homecare, and beauty brands in many markets, announce the development of two new flexible packaging solutions containing both virgin polyethylene (PE) and high amounts of post-consumer recyclate (PCR). One of the pouches – developed in value-chain co-operation and containing 30% Ecoplast-produced PCR – will be presented at the K 2019 in October.
Achieve better packaging circularity while maintaining shelf appeal
Flexible pouches are among the fastest growing segments of the packaging industry. Like other flexible packaging forms such as bags, sachets, films, liners, and wraps, pouches safeguard the integrity, quality, and longevity of pack contents while offering value-added functionality and convenience. Stand-up pouches have the additional advantage of being ideal carriers of on-pack brand and product messages with special shelf appeal.
Yet, despite the many benefits for consumers and brand owners, in the future, flexible packaging solutions must go beyond their current functionalities. Recyclability must be “built in” to the packaging itself. This is necessary to reduce the overall environmental impact, generate less waste, and to ensure that the valuable resources needed to produce such packaging are kept in the use cycle as long as possible.
In many parts of the world, regulatory actions to increase recycling rates have or will soon take effect. Brand owners and packaging producers alike are keen to increase the share of PCR in their own applications, yet they require viable solutions that appeal to end consumers as well. The challenge for the industry is to redesign flexible packaging solutions and novel packaging materials for the most popular applications – notably pouches, and sachets – in order to effect truly meaningful reductions in the volume of post-consumer plastic waste.
Value-chain collaboration yields new flexible pouches with up to 35% recyclate
Value-chain co-operation is driving the circular economy of plastics. Among other sustainability-related efforts, brand owners and packaging producers are seeking ways to lower the overall CO2 footprint of packaging. Co-operation among Borealis, Borouge, Henkel, and several value-chain partners has now yielded two novel pouches with excellent market potential. Each contains both virgin PE and larger amounts of high-quality recyclate made by Ecoplast.
The new flexible pouches are a response to strong market demand – particularly in the fast moving consumer goods sector – for more numerous and varied consumer applications incorporating higher amounts of PCR. Increasing the share of recycled materials in packaging is an essential component of enhanced plastics circularity. As part of its diverse circular economy-related efforts, Henkel, for one, has introduced a dedicated range of adhesives optimized to achieve this purpose.
The Full PE + 30% PCR made by Ecoplast
The first new pouch has been developed in close collaboration among Borealis, Borouge, and the Henkel Laundry & Home Care business unit, and also using adhesive solutions developed by Henkel’s Adhesive Technologies business unit. While the pouch is based on the Full PE Laminate solution launched by Borealis and Borouge several years ago, it features a new material combination: virgin PE paired with 30% Ecoplast-produced PCR-PE recyclate, an unusually high PCR level for a flexible consumer packaging application. The pouch also contains Henkel Adhesive Technologies’ innovative adhesive from its newly introduced RE range, which is “designed for recycling” and allows for homogeneous laminates to be recycled mechanically with excellent results.
Among other products, Henkel plans to use the new pouch for its leading Persil detergent brand in select regions. This is proof positive that a pack containing a high amount of recyclate, and laminated using an adhesive compatible with mechanical recycling, can fulfil the most sophisticated consumer demands when it comes to look and feel, functionality, and convenience. Moreover, it offers the added bonus of reassuring consumers that they are helping the environment with the purchase of this packaging format.
The Full PE + 35% PCR made by Ecoplast
A second newly-developed pouch offers an even higher level of recyclate in its mix. This Full PE Laminate stand-up is composed of both virgin and recycled ingredients: BorShape™, Anteo™, and Queo™, along with 35% post-consumer recycled low density polyethylene (r-LDPE) made by Ecoplast.
Using this novel material offers attractive down-gauging options to producers. It also reduces the amount of raw materials required in production, and in particular virgin raw material, as the share of recyclate in the mix is significantly higher. All things considered, this pouch offers a lower overall CO2 packaging footprint. What is more, using Henkel’s dedicated range of RE adhesives in the production process makes it possible to obtain an excellent quality of recyclate when recycling this product, and enables re-use and/or additional recycling cycles.
This second prototype pouch is currently being developed and tested by a value chain consortium, with each partner contributing their respective expertise and experience to ensure joint success:
Borealis and Borouge: Combining proprietary Borstar® bimodal PE technology and Borealis resins forms the foundation of PE films with excellent performance characteristics, efficiency, and pleasing aesthetics. Anteo™ is the key ingredient for higher performance and more sustainable multilayer applications. The plastomers brand Queo™ delivers a range of unique performance attributes, including superior sealing, flexibility, compatibility and processability.
Ecoplast was acquired by Borealis in 2018. As a leading Austrian plastics recycler, it produces high-quality LDPE and high-density polyethylene (HDPE) recyclate, processing around 35,000 tonnes of household and industrial plastic waste each year.
Henkel: The Henkel Adhesive Technologies business unit offers a unique portfolio of breakthrough innovations including its RE range of adhesives designed for mechanical recycling and recycled content, tailor-made solutions and strong brands in adhesives, sealants and functional coatings. Together with the Henkel Laundry and Home Care business unit, the company supports strong performance in design for circularity in flexible packaging – particularly in increasing the percent of post-consumer recycled content.
GEA: As experts in developing innovative solutions for smart food processing, GEA partnered with Borealis and other value-chain partners in 2016 to develop the original Full PE Laminate solution. GEA produces stand-up pouches at high packaging speeds on its vertical form fill and seal (VFFS) pack line.
Hosokawa Alpine is a leading technology supplier specialised in developing, engineering and installing machines and systems for process technology and blown film extrusion for customers around the world. Hosokawa Alpine uses Borealis resins on its five-layer line with inline machine direction orientation (MDO) and patented TRIO system to produce PE films so innovative and efficient that they can function as replacements for conventional substrates in complex pack structures.
HP Indigo digital presses are designed with the environment in mind with a clear strategy for sustainability that increases the benefits of digital print, including reducing material waste and power consumption for commercial, label and packaging applications.
“The success of this value-chain collaboration shows that our K 2019 motto, ‘Building Tomorrow Together’ is truly the best way to achieve greater plastics circularity,” claims Geert Van Ballaer, Borealis Head of Marketing Consumer Products. “We think of this project as a kind of ‘Full PE Laminate 2.0’, and are glad to have partners eager to work with us in taking it to the next level.”
“Thanks to our joint efforts and extensive collaboration with partners like Borealis, we are bringing to the market the first adhesive from our RE range that can be mechanically recycled, and – along with polyolefin plastic films – be incorporated into the loop for re-use,” explains Marcin Lapaj, Global Business Development Manager for Circular Economy at Henkel Adhesive Technologies. “As we develop new products and packaging forms, we strive to ensure that each makes some contribution to enhanced sustainability. We are pleased to cast the spotlight on this novel packaging solution at the K Fair and are confident that consumers will embrace this significant contribution to plastics circularity.”