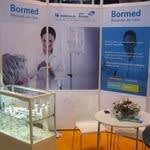
Visitors to the stand will be updated on manufacturing and user advantages made possible with the latest additions to Borealis and Borouge’s portfolio of dedicated Bormed polyolefins for healthcare.
Bormed LE6601-PH for the development of transparent, simple to squeeze ampoules Bormed LE6601-PH was spotlighted at Pharmapack 2011 and has since proven itself in the market for eye, ear and nose drop treatment ampoules as well as dip-tubes in pharmaceutical sprays.
Packaging converters benefit from trouble-free conversion on standard blow moulding and blow, fill and seal (BFS) machinery. Wall thickness and ampoule weight are easy to control thanks to Bormed LE6601-PH’s optimised molecular weight distribution that produces material with low swell. This allows difficult shapes to be formed, while ensuring straightforward dosing to simplify production of consistent, high quality ampoules. The easy processing creates less waste and a low energy requirement during extrusion.
This high density polyethylene (HDPE) creates productivity improvements for manufacturers of, for example, two-part syringe plungers, caps and closures, etc. With a melt flow rate (MFR) of 31, Bormed HE9601-PH delivers a flow rate improvement of up to 2.5 times that of comparable alternatives. The injection moulding process, in particular of components with complex design parameters or long flow lengths, is simplified.
Converters see faster production and increased throughput at decreased pressure and temperature. Energy and mould maintenance requirements are both lowered providing a cost advantage. These benefits are gained without compromising the performance of medical devices and pharmaceutical and diagnostic packaging.
Another Bormed development leading the way in creating new opportunities for improved performance and efficiency in the healthcare market is Bormed SC820CF for primary and secondary medical pouches. This random heterophasic polypropylene (PP) copolymer for cast- and blown film applications combines softness with toughness and is steam sterilisable. It also maintains good optical and mechanical properties after retorting.
Bormed SC820CF is intended as a blending component or co-extrusion layer for primary pouches with contents such as intravenous (IV) solutions, nutrition and dialysis fluids. Furthermore it is used as part of the solution for secondary wrap films for dust and vapour barrier and protection. This new material contributes to all PP pouch solutions, which serve as a viable alternative to commonly used glass bottles or polyvinyl chloride (PVC) pouches.
“Our commitment to the healthcare market spans more than three decades and will continue far into the future,” says Rainer Höfling, Borealis Vice President of Business Unit Moulding. “We provide our customers with the utmost confidence when using our dedicated Bormed materials in their applications.”