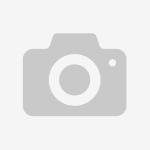
Visitors to Stand 54 can experience first-hand why Borealis` materials are taking a leading position in the development of interior and exterior automotive parts that meet the manufacturing, performance, weight-saving and fuel-reduction challenges facing the industry. For two consecutive years, Borealis` pioneering solutions have been formally recognised by the Society of Plastics Engineers (SPE), winning prizes in the 2006 and 2007 Automotive Awards.
The result of close co-operation between Borealis, Tier One suppliers and automotive OEMs, Borealis will showcase technological breakthroughs, single-material solutions and differentiation opportunities based on its Daplen thermoplastic olefin (TPO), Nepol long glass fibre and XMOD short glass fibre modified compounds. These include:
- Step change innovation: a 100% plastic module solution to replace the use of metal for the rear seat carrier on a future BMW Series. Granted the "2007 Grand Innovation Award (Body Interior)" by the SPE, the use of Borealis` pioneering XMOD GD302 HP in a sandwich structure with Expanded Polypropylene contributes significantly to part weight reduction and a streamlined manufacturing process by reducing the total number of parts. This lowers the overall car weight, thereby reducing CO2 emission and fuel consumption.
- Innovative market differentiation and weight-reduction benefits for the "2007 Car of the Year" FIAT 500. A one-material solution for the Fiat 500 dashboard using Daplen EE168Al offers superior interior aesthetics, excellent scratch resistance, safety and manufacturing improvements through an excellent impact/stiffness ratio, and significant lower weight without compromising on performance.
- Smart fortwo: the first commercialised car to have full body panels manufactured from PP. Borealis developed Daplen ED230HP to meet the cost-effective production targets and aesthetic, safety and environmental requirements of the latest Smart vehicle. The injection moulded PP exterior body panels provide a 15% reduction in overall vehicle weight. They also increase quality perception through more narrow gap tolerance between parts and an excellent impact/stiffness ratio. It was a joint winner of the SPE`s 2007 Body Exterior Automotive Award.
- Our comprehensive plastics solutions are leading in areas such as zero gap tolerance for bumpers and off-line painted body panels - explains Franz Zaengerl, Business Development Manager Automotive at Borealis. - Borealis is committed to helping the automotive industry meet the manufacturing, performance and environmental challenges of the future. We work closely with our customers to develop lightweight, one-material solutions that meet and advance performance and environmental considerations. Our planned investments in new extrusion lines and compounding facilities in Brazil and China respectively further reinforce our ability to provide the high performance materials required by automotive markets - he adds.
With an in-depth understanding of the value chain and a focus on customer needs, Borealis provides innovative, value creating polypropylene solutions with optimum performance for interior, exterior and under the bonnet applications.