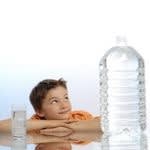
The SBO Compact2 delivers high quality and performance levels equivalent to those of the SBO Universal blow-molder range. The latest evolution is industrially improved and more robust, while performing even better because of electrical stretching.
The final quality of the bottle is determined by the quality of preform stretch-blowing using bi-orientation. Throughout the process, the aim is to ensure maximum process precision and repetitiveness, while obtaining optimal production speed.
To improve the process, Sidel developed a new stretch-blowing system for the preform. Traditionally, the pneumatic process uses hydraulic actuators to drive the vertical movement of the stretching rod. This was replaced by an electrical process by installing a servomotor and ballscrew assembly.
The new stretching console provides many benefits. It enables constant control of the stretching position and speed, which ensures perfect repetitiveness of the process. The production is also more flexible: it works for a variety of bottle sizes because it is no longer necessary during format changeovers to manually adjust the pre-blowing and blowing start detectors. Finally, the maximum stretching speed increases from 1 m to 1.3 m per second, enabling higher production speeds. These benefits make the SBO Compact2 range a reliable and more flexible solution.
In addition to electrical stretching, further developments improving reliability include preform feeding and Human Machine Interface (HMI). The machine is more productive due to new, longer orienting rollers that secure preform stability and infeed fluidity. Additional panel functions make the machines more ergonomical for operators. Format change-overs are now easier to carry out because the stretching parameters are managed directly from the HMI and no longer within the machine.
These performance improvements are already appreciated by the first customers in South Africa and South America purchasing SBO Compact2 systems. More than ten SBO Compact2 blow-molders are currently being installed.
Whatever the product, water, carbonated soft drink, juice, dairy product, detergent, cosmetics, the SBO Compact2 can blow simple or standard shapes using either PET or other plastics from 0.2 liter to 10 liter containers. It can also manage the blow-molding of complex packaging, such as asymmetric shapes or flat containers, through the preferential heating process with a possible neck orientation. The DeepGrip™ packaging innovation, a box-conforming technology, is equally supported by the SBO Compact2 platform.
As a natural evolution of the SBO Compact range, the new SBO Compact2 linear blow-molders, which include the SBO 4, SBO 4 PH, SBO 3 XL, SBO 3 PH and SBO 2 XXL PH, now run at speeds ranging from 2,400 to 7,200 bottles per hour. All SBO Compact2 blowers systematically benefit from a 100-hour mechanical run-off as a minimum, including one-hour bottle production. This guarantees equipment quality and production efficiency. Machine installation, start up and commissioning can be secured and completed in less than ten days.
As part of these continued improvements, Sidel is working to increase the process capabilities further to manage any type of container, including wide-mouth jars and heat resistant packages.