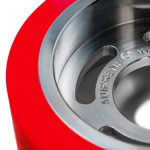
Specialty chemicals company LANXESS will be showcasing its premium products for the polyurethane industry at UTECH Europe 2018 from May 29 to 31. The new Urethane Systems business unit will be represented at the conference for the first time. “We want to use this major event in the global polyurethane industry primarily to strengthen our position as a customer-focused urethane systems provider. The focus is on our broad range of prepolymers with very low free isocyanate content. This technology opens up new opportunities for our customers, especially in terms of performance and safety,” explains Dr. Markus Eckert, Head of Urethane Systems. Other key topics include material alternatives to MbOCA-cured cast systems and blocked systems for a range of cast and coating applications.
As one of the leading manufacturers of bromine and phosphorus based flame retardants, LANXESS’s Additives business unit offers solutions for all types of polyurethanes. The product innovations presented at UTECH Europe include flame retardants, plasticizers, crosslinkers, catalysts and hydrolysis stabilizers. The focus there is on new flame retardant solutions from the Levagard, Disflamoll and Reofos product ranges, which have proven themselves in rigid and flexible foam applications based on polyurethane. The business unit also introduces Stabaxol L, the first product in a new range of low-emission hydrolysis stabilizers. “Our new oligomeric flame retardant solutions can help address the increasing requirements for flexible foams and meet our customers’ demands for low fogging and low emission additives,” explains Dr. Heiko Tebbe, Manager Application Technology Polymer Additives at the LANXESS Additives business unit.
Urethane Systems: Broad portfolio of low free (LF) isocyanate prepolymers
Compared to other manufacturers, LANXESS Urethane Systems has one of the broadest portfolios of prepolymers with low free isocyanate content for cast elastomers. Adiprene LF prepolymers are based on TDI, MDI, HDI, IPDI, and pPDI diisocyanates, with free monomer content usually below 0.1 percent. “Our low free prepolymers meet the latest regulatory standards with regard to health, safety and environmental protection, so that the processor can minimize required protective measures. At the same time, they help our customers to improve the mechanical performance of elastomer components and to produce them economically,” explains Eckert.
Better properties than MbOCA-cured elastomers
In particular, Adiprene LF MDI prepolymers, together with the aromatic diol curing agent Vibracure 2101, are an alternative to TDI and LF TDI prepolymers cured with MbOCA (4.4′-Methylene-bis(2-chloroaniline)). The use of MbOCA within EEA countries has recently been severely restricted and regulated by the European chemicals regulation REACH. “Our urethane systems meet all REACH requirements, and produce elastomers with high elasticity and improved resistance to abrasion, impact, and hydrolysis, while using the same processing equipment. In addition, they are easier to process because of their lower viscosity,” says Eckert. The pot life can be long to help with molding large parts, and can be catalyzed for higher productivity.