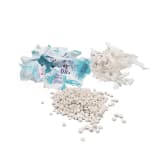
Keycycle, a subsidiary of the Erema Group, has worked together intensively for two years with the Spanish company Cadel Deinking to further develop the innovative process of removing printing inks from the surface of plastic. This has proved successful, because there are now several deinking lines in operation at customers' sites, where they are proving their efficiency in processing printed inhouse and post industrial film waste. Having acquired the Cadel Deinking brand, Keycycle will now continue to develop the technology and market the deinking process under the Keycycle Deinking brand.
"We have already been exclusively responsible for the worldwide distribution of this patented technology since January 2021, including the operation of the pilot plant together with Cadel in Sant Vicente del Raspeig (Alicante). By acquiring the trademark rights, we are now taking the final step of integrating this process technology into our product portfolio," says Michal Prochazka, Managing Director of Keycycle. This technology is a milestone in safely feeding back into the production process recycled pellets made from plastics that were originally printed. "The product not only delivers top quality, it now also meets industrial standards," explains Prochazka, referring to the new larger deinking line with a throughput of 1,200 kilograms per hour, an innovation that was recently presented for the first time at K 2022. With plants on this scale, the Keycycle deinking process also opens the door to the post consumer recycling segment, where the removal of printing inks enables another significant quality upgrade for the recycled pellets.
How the Keycycle deinking process works
During the decolourisation process, the ink is dissolved from the surface of the shredded film or regrind material. Only water-based chemical components are used, which makes the deinking process particularly environmentally friendly. The material is then fed into the recycling extruder. Of the eight plants ordered since the market launch, five are now in operation at customers' sites, where they are delivering very impressive results.
Keycycle demonstrated how this works to visitors at K 2022: In the Erema Circonomic Centre, inhouse waste film and post consumer film were recycled both after pre-treatment in a deinking plant and without deinking. The difference in quality of the two streams of recycled pellets was clearly visible.
The Cadel company continues to operate as Cadel Recycling Lab, dedicated to its core competence of developing new innovative technologies for plastics recycling plus laboratory and software techniques for decontamination assessment.
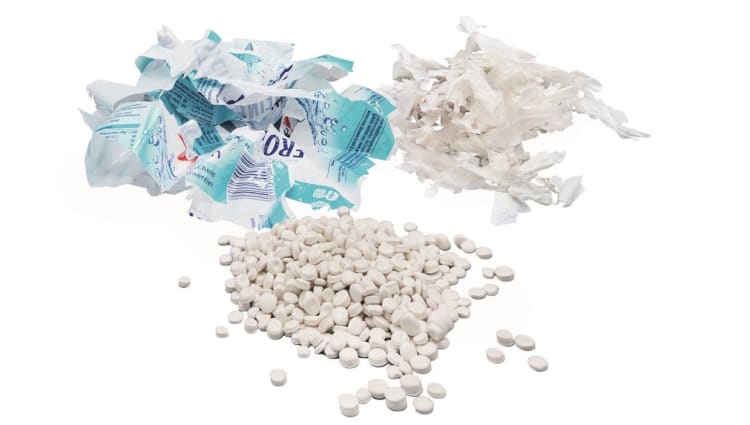
Heavily printed film (left) is colourless following the deinking process (right) and as a result can be processed in the recycling extruder to make high-quality recycled pellets (bottom).