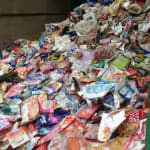
"I question whether we should be burning this so-called 'unrecyclable' waste plastic," asserts Director Keith Freegard. "There's a danger that if materials which are currently not recycled, such as post-consumer multi-layer films, black trays and heavily-printed flexible packaging, find their way down the energy-from-waste route, then they get 'locked in' to that waste disposal system for a long time due to the industry's long-term investment strategies and inflexible long-term waste supply contracts."
This approach, he warns, could stifle innovative redesign to create new recyclable packaging products and hold back development of new technology that allows existing plastic packaging materials to be captured, sorted and recycled.
As an example, Keith highlighted Axion's Shredder Waste Advanced Processing Plant (SWAPP) at Trafford Park where plastics are extracted from automotive shredder residue (ASR) and turned into high-grade recycled polymers used in new products, such as vehicle components.
"A few years ago, plastic in ASR from end-of-life vehicles was thought to be unrecyclable and sent to landfill. Pull-through from some enlightened end-users wanting recycled products, alongside increasing landfill tax, has helped to create the drivers needed for investment in large-scale processing plant. It's a great closed-loop success and, with support from the whole value chain, there's no reason why this couldn't be replicated with other so-called 'unrecyclables'," he says.
"Similar market drivers have created the need for product development initiatives such as the REFLEX project, born out of a shared desire to improve the recyclability of flexible packaging across key industry stakeholders, like global consumer brands, polymer producers and film converters."
Crucially, he points out, it is essential that materials currently destined for EfW units or landfill can be easily diverted to novel and new recovery processes where they will acquire more value and move up the waste hierarchy.
What's needed, according to Keith, are stronger links between political will, demand-led legislative drivers and technological developments that will encourage greater stakeholder involvement and the creation of fresh markets for 'tomorrow's new materials'.
"By working together, we can make intelligent design choices that deliver circular material flows and make truly sustainable products," he adds. "In doing so, the 'unrecyclable' plastics will move into the 'recyclable' category."