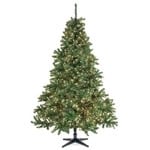
Professor Jan Bayens, University of Warwick, have devised a new technique which could process 100% of Christmas and other household plastic instead of the tiny fraction that currently actually gets processed -- typically only 12% of such waste is truly recycled often the rest is often put into land fill or simply burnt as fuel.
Some plastic still goes straight to land fill but householders currently spend a great deal of effort separating out the rest of their plastic waste believing it will be recycled yet typically only 12% of "Municipal Plastic Solid Waste" is truly recycled. It is often simply too time consuming to separate out and clean the various types of plastic of their persistent labels or other problems, as that requires significant laborious human intervention. An additional problem is that often objects are made of more than one plastic that would require different treatments.
However University of Warwick engineers have come up with a simple process that can cope with every piece of plastic waste and can even break some polymers such as polystyrene -- back down to its original monomers (styrene in the case of polysterene).
The Warwick researchers have devised a unit which uses pyrolysis (using heat in the absence of oxygen to decompose of materials) in a "fluidised bed" reactor. Tests completed in the last week have shown that the researchers have been able to literally shovel in to such a reactor a wide range of mixed plastics which can then be reduced down to useful products many of which can then be retrieved by simple distillation.
The products the Warwick team have been able to reclaim from the plastic mix include: wax that can be then used a lubricant; original monomers such as styrene that can be used to make new polystyrene; terephthalic acid which can be reused in PET plastic products, methylmetacrylate that can be used to make acrylic sheets, carbon which can be used as Carbon Black in paint pigments and tyres, and even the char left at the end of some of the reactions can be sold to use as activated carbon at a value of at least £400 a tonne.
This research could have a significant impact on the budgets of local authorities and produce considerable environmental benefits. The lab scale tests concluded this week have successfully produced distilled liquids and solids that can be taken away by the bucket load for processing into new products. The University of Warwick engineers are now working with the University's technology transfer arm, Warwick Ventures, who expect that their work will be of great interest to local authorities and waste disposal companies who could use the technology to create large scale reactor units at municipal tips which would produce tanker loads of reusable material.
The lead researcher on the project, University of Warwick Engineering Professor Jan Baeyens, said: "We envisage a typical large scale plant having an average capacity of 10,000 tonnes of plastic waste per year. In a year tankers would take away from each plant over £5 million worth of recycled chemicals and each plant would save £500,000 a year in land fill taxes alone. As the expected energy costs for each large plant would only be in the region of £50,000 a year the system will be commercially very attractive and give a rapid payback on capital and running costs."