User-friendly, efficient operation and maintenance
Stadler’s innovative approach includes the use of technologies to facilitate operation and maintenance of the plant, as well as comfort for the operators.
An advanced load cell system has been installed for monitoring the quantity of incoming material and the quantities of the different materials stored in the bunkers ready for baling. This enables the operator in charge of the baling presses to keep track of exactly how much material is contained in each bunker and produce a precise number of bales for each product.
A new local maintenance system provides operators with a mobile panel that they can connect in each area of the plant to control all the machines in the section. Detection sensors on motors facilitate data collection and analysis for preventive machine maintenance. In addition, the entire plant can be monitored remotely with dedicated software that collects and records more than 1,000 signals at a time to generate periodic reports valuable for predictive maintenance.
The sorting cabin is equipped with an efficient air conditioning system that maintains a comfortable working environment year-round, providing 10 air changes per hour with fresh air from outside.
“Circular Plastic is a truly impressive facility with all its machines and optical sorters,” says Flaviano Fracaro. “What we appreciate most is the layout's space management, with walkways that make all the machines accessible and the entire plant easy to navigate, ensuring excellent access for maintenance. Additionally, thanks to the various management systems for operators, it is very easy and intuitive to control and manage the entire facility.”
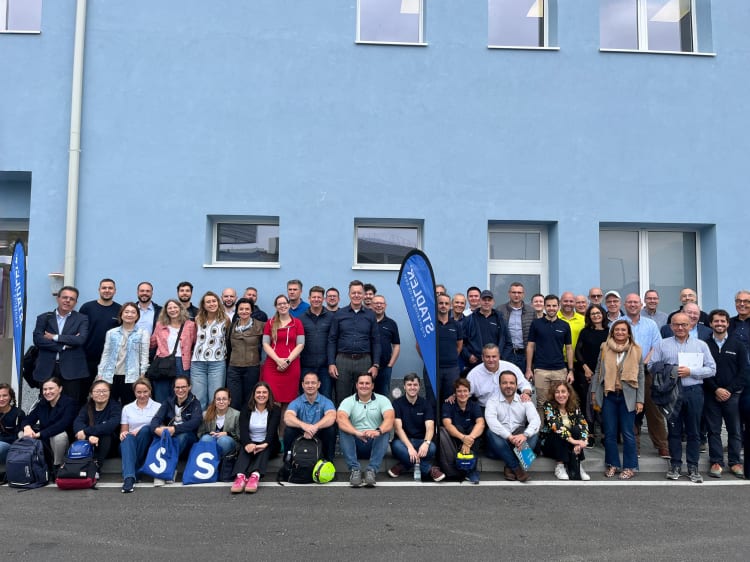
Stadler’s holistic approach - key to the success of a complex project
The Circular Plastic project presented challenges at every stage that required Stadler’s extensive experience - from designing to ensuring effective communication across all parties involved in the implementation, all the way to final tests and commissioning to ensure the plant operates as required to deliver the desired consistent high quality.
“In the design stage, we had to study how to optimize space and distance to assemble all the machines in the building allowing for future maintenance and upgrading,” explains Paolo Cravedi. “Then, during the assembly phase, the challenge was coordinating more than 100 people from 20 companies to assemble the plant and all auxiliary systems. Finally, once the plant was assembled, we had to ensure it could manage the high incoming material flow of 20 t per hour, that the line had the mechanical capacity to process this inflow without material blockages or plant stops and deliver the very high level of quantity and purity of all outgoing products.”
“At every stage, Stadler's teamwork and organization were crucial in defining and implementing the project. We appreciated Stadler's ability to adapt the layout and design to our needs, leveraging their extensive experience in plant engineering to inform technical decisions. The construction phase coincided with a period of great difficulties in transport services with numerous delays. Despite these challenges, Stadler was able to adapt and reorganize the work, maintaining very fast construction and commissioning times. Completing such a complex plant in a short time frame is no easy task, but Stadler was highly efficient in assembling the entire line and coordinating all suppliers to ensure the project was completed safely and on time. Stadler’s excellent organization is a key factor in the success of such a project,” concludes Flaviano Fracaro.