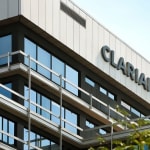
In order to work effectively in polymers that are processed at temperatures of 300°C or higher, masterbatches must be specially formulated using not only the same high-temperature base material, but also special pigments and additives that can stand up to extreme levels of heat and shear. Compounding and extrusion equipment must also be configured to operate under these extreme conditions. Three Clariant Masterbatches plants in the United States –Holden, Massachusetts, Lewiston, Maine, and Albion, Michigan – already have vast knowledge and experience in working with both engineering and high-temperature materials. Capabilities in Asia have previously been more limited, focusing mainly on engineering materials (like ABS, polycarbonate and certain nylons), which are processed at moderate temperatures. Customers in this region have therefore often had to source the more advanced products from overseas and thereby facing longer product development and delivery times. That is about to change.
"Global demand for high-temperature plastics and compatible masterbatches is booming" says Jeff Saeger, who heads the expansion program for Clariant. "Fueled by new products in the automotive, small consumer electronics and electrical markets, the use of engineering materials is growing at annual rates of 7 or 8%, well above the growth rate of the plastics industry as a whole. Clariant has state-of-the-art capabilities in the United States to handle these materials and will now leverage that experience and expertise around the world."
In Shanghai, where Clariant is implementing the full range of equipment, and procedures required for engineering and high temperature resins, new production lines and associated capabilities will be in place by the end of 2016. In the United States, the company installed equipment for processing fluoropolymers in Lewiston, Maine, in late 2015, and new lines for specialty engineering compounds and black masterbatch for high-temperature resins will be added in Holden, Massachusetts, beginning in first quarter 2016.
Without high-temperature masterbatches, part producers have only a couple of choices. They can mold the parts in the resin's natural color and then paint them, or they can use pre-colored compounds. However, Saeger explains, many companies need relatively small quantities of engineering and high temperature materials, making both these methods un-economical or even unavailable. The major resin producers today offer only a narrow range of standard colors and usually will not produce small quantities of special colors. Smaller custom compounders can produce smaller volumes but at higher costs.
The solution, he says, is "natural plus." Processors buy readily available natural-color resin and then add a color concentrate (masterbatch) precisely formulated to achieve the exact finished color required. The advantages of this approach are many. The high cost of small quantities of custom-colored resin is avoided. Processors can buy larger quantities of natural resin and also have less capital tied up in an inventory of colored resin that may only be used occasionally. Storage space requirements are minimized. Production benefits accrue from centralized drying and handling of natural resin and faster color changes. Manufacturers are also much more flexible in responding to changing consumer color preferences.
The new investments are expected to be especially beneficial to manufacturers of electrical products and appliances, since many of these devices and the components in them contain engineering plastics that need to meet flammability-resistance standards promulgated by Underwriters Laboratories (UL).