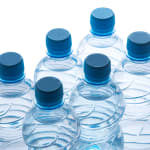
High-density polyethylene (HDPE) is widely used in the manufacture of bottles, pipes and containers because of its strength and rigidity, but also in personal care products, detergents and industrial fluids because of its durability. Another major application is the manufacture of bottle caps and milk bottles. A recycle stream already exists due to changes in deposit regulations and the attachment of bottle caps to the bottle. The caps go through the same washing systems as PET, are then separated in the float-sink tank and can be further processed. As a result, they also meet the high-quality requirements for bottle flakes.
If treated with the Gneuss "Super Clean Process", the regrind can be reprocessed back into a bottle cap, thus closing the recycling loop. The Gneuss OMNImax recycling system used in this process has undergone multiple challenge tests and has been awarded several food contact approvals/LNOs.
The technology does not require any upstream or downstream process steps. This is of great importance for polyethylene, as it can only be treated in other processes at very low temperatures and requires long residence times due to the slow diffusion processes involved.
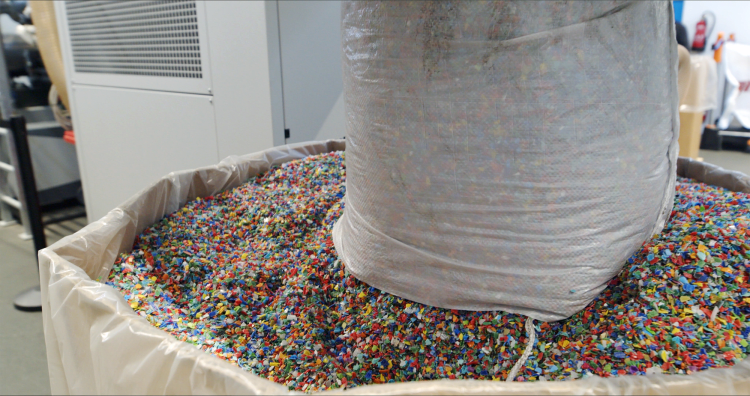
Regrind from HDPE bottle caps
The OMNImax purifies the polymer by subjecting it to highly efficient degassing using an MRSpure extruder and a robust vacuum system to remove volatile contaminants. The Multi Rotation System (MRS) is preceded by a melt extruder, which separates the plasticizing and degassing/ deodorizing/ decontamination process steps so that the process parameters can be optimized individually for each process step.
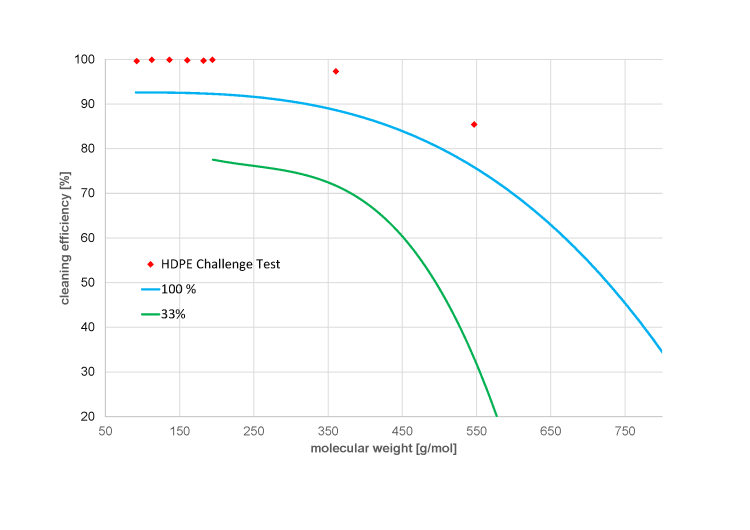
Results of the HDPE challenge tests, submitted 2024
Downstream of the melt extruder, the RSFgenius filtration system removes hard contaminants by ultra-fine filtration. Its fully automatic operation with guaranteed pressure and process consistency cleans the contaminated screens directly before they re-enter the melt channel, so that the screens can be automatically reused up to 400 times.
Typical filtration finenesses in HDPE recycling are 125-300 µm. In addition, for milk bottle recycling, the material can optionally be fed into the extruder via a 3C Rotary Feeder.
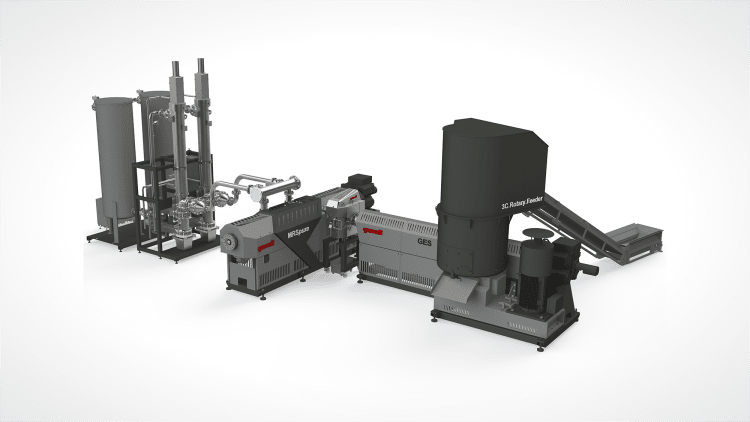
OMNImax recycling system with upstream single screw
The flexibility of the recycling system is outstanding: the OMNImax system compensates fully automatically for variations in the plastic waste to be processed in terms of moisture, contamination, viscosity, bulk density, etc. by adjusting the process parameters so that material of consistently high quality can be produced. Material changes, e.g. for batch changes, are possible within minutes due to the short residence time, so that the flexibility requirements of a new recycling plant are fully met, and production interruptions can be reduced to a minimum. This unique feature makes the OMNImax recycling system exceptionally cost-effective, especially in applications where food contact or odor reduction is required.
In addition, the technologies developed and patented by Gneuss are characterized by:
- Compact design, small footprint
- Short residence time
- High flexibility
- Low energy consumption
- High economic efficiency
- High cleaning efficiency (super-clean), also for food contact