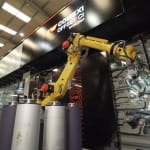
Comexi, a global supplier of solutions for the flexible packaging printing and converting sector, and Ellerhold, a company specializing in the production of advertising, labels, and packaging materials for a wide range of applications, have signed an acquisition agreement for an Offset CI printing press. The use of Comexi's offset central impression printing technology and EB (Electron Beam) curing system will allow Ellerhold to improve its efficiency while providing the highest level of printing quality.
This Central Impression printing press offers significant advantages, including increased efficiency, improved sustainability, and unmatched print quality, enabling Ellerhold to strengthen its leadership in the market. This milestone underscores the growing success and trust in Comexi's Offset technology, as more clients recognize its value and innovative capabilities.
“The Comexi Offset CI is the best option for a printer looking for sustainability and higher efficiency. This technology allows Ellerhold to operate without solvents, providing the highest printing quality even for the most complex designs that could be frequently grouped, printing multiple SKUs in the same run. This practice saves costs, time, and waste while increasing productivity,” explains Felip Ferrer, Technical Sales Director for the Offset Printing division at Comexi. This is a solvent-free hybrid printing press that combines offset and flexo with a central impression cylinder (CI), using Electron Beam (EB) curing inks. It encompasses the advantages of Offset printing and the safety of low migration and low odour photoinitiator- free EB inks and coatings approved for food packaging.
The machine is equipped with robotic sleeve changeovers and automated colour pre-setting and colour control. The new model Offset CI Evolution provides a higher automation level, unbeatable printing quality, and the best color consistency.
The Comexi technology offers the best solution to maximize the Extended Color Gamut (ECG) process: perfect register, highest resolution, and quality printing in solids, highlights, and fadings. Not limited to ECG, this press can easily handle direct colors as well, thanks to automatic washing in all units.
The equipment includes one flexographic unit in the last position capable of applying high- opacity whites for transparent films and EB coatings for finishing on surface jobs, which gives the best surface protection against scratches, heat, and chemicals, either matte or glossy.
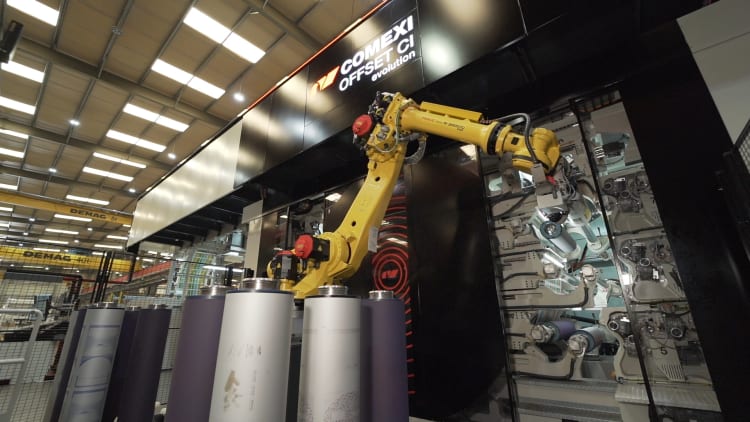
The factors that make Comexi Offset CI the best sustainable printing solution:
- The EB curing system consumes low energy and provides high productivity, ensuring perfect ink curing at maximum speed.
- EB inks and coatings are the optimal solution to replace solvents, reducing VOCs and CO2 emissions, consuming less ink and energy, and creating a safe environment by reducing fire risks. VOC-free inks do not require peripheral equipment to recover solvents, making it a perfect solution for greenfield plants.
- The EB inks do not dry in the printing press and can remain in the machine for a long period of time. This, together with the advantages of using ECG, reduces the number of cleanings and the changeover process, increasing efficiency
- EB Offset printing does not apply heat to materials. In combination with central impression, it enables high-speed and perfect register printing on thinner materials. It can handle a wide range of substrates to be used for many applications in labels and flexible packaging.
- Using cost-competitive lithographic aluminum printing plates (5 to 10€ each) that are imaged in a CTP (computer-to-plate) in a few minutes and are fully recyclable after use. This flexibility can be used to avoid printed stocks by printing on demand, similar to digital printing solutions but more efficient thanks to the higher speeds of 300 m/min and the wider web of 1100mm.
- The low-cost plates, faster pre-press, and capabilities in ECG allow multiple SKU printing, making short runs efficient. Grouping several short-run designs into a single long run increases productivity while reducing waste and changeover time required for individual SKUs.