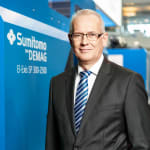
Gerd Liebig, CEO of Sumitomo (SHI) Demag Plastics Machinery GmbH, outlined how high-quality connector production can be designed cost-effectively and sustainably in the future in a talk held during the LAPP trade press event. He drew a bridge from the trends in customer requirements and machine generations to the collaboration with partners and corresponding make-or-buy strategies, right through to the resulting requirements for connectivity, miniaturisation and increased reliability of the connectors.
Liebig reported on market trends characterised by an increasing demand for sensors and functionalities, for example for interior equipment in the automotive sector. “The development is heading towards greater connectivity and machine condition monitoring within the smallest possible installation space to achieve the lowest possible footprint in the production unit with regard to sustainability,” said Liebig.
On this basis, he analysed product trends such as standardisation of connectors to simplify processes and reduce costs, and the demand for smaller connectors with higher functionality, as well as the integration of sensors, cables and connectivity.
Sumitomo (SHI) Demag is meeting these challenges by driving forward with the digitalisationof its machines. The fully electric IntElect series for regulating, controlling, monitoring and integrating automation and peripheral systems has an OPC-UA interface. They also have their own web-based software solution "myConnect". This central platform gives customers direct access to a wide range of fully networked services for their machine.
The third largest manufacturer of injection-moulding machines in the world is currently working on developing assistance apps, a system for setting up and optimising processes, introducing a material and knowledge database and integrating simulation tools for expanded configurations and in-depth insights into the processes. The aim, says Liebig, is an intelligent machine that can independently make predictions about part quality, machine wear and failures, and perform optimisations online.
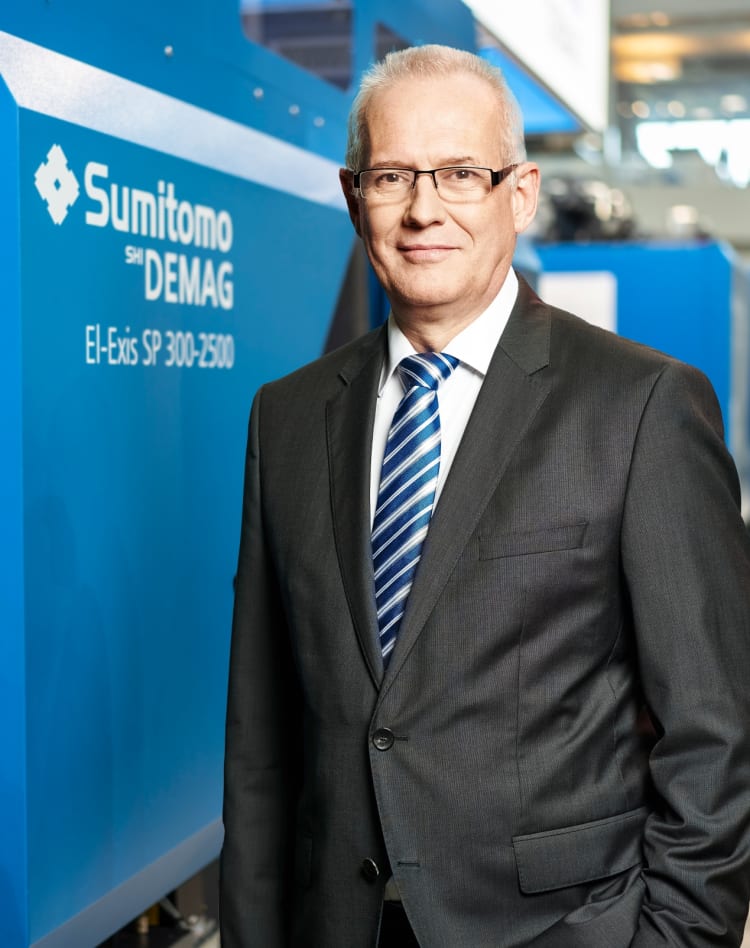
Gerd Liebig, CEO of Sumitomo (SHI) Demag Plastics Machinery GmbH
“This aspiration is not an end in itself, but serves to produce machines with high flexibility in a cost-optimised manner,” reports the CEO. This is achieved by a combination ofthe company's high-quality work in Germany supplemented by cost efficiency in Asia. “Our focus is clearly on fully-electric machines for the packaging and medicine sectors. We impress with differentiated, high-quality technology rather than complex, low-quality machines, and offer our customers high efficiency with unique products.”
Particularly in connection technology, Liebig expects increasing demand for sensors and functionality, for example for interior equipment in the automotive sector. It is therefore essential for connectors to be further standardised to simplify processes and reduce costs. Smaller connectors with better functionality are also the order of the day, given the increasingly compact components.
Sumitomo (SHI) Demag’s focus is on the fully electric mechanical engineering series IntElect. “The market has greatly picked up since the beginning of this year, mainly driven by the automotive and consumer sectors, as many companies are investing in machinery there again,” said Liebig. "Our decision four years ago to consistently rely on fully electric and energy-efficient machines from the IntElect series has paid off. Turnover will thus continue increasing in the coming years, as more and more governments are pushing for energy-efficient production.”

The IntElect series, a fully electric and energy-efficient injection moulding machine from Sumitomo (SHI) Demag, the global market leader in fully electric machinery