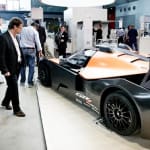
Lightweight construction plays an especially important role within the context of e-mobility in the automotive sector. “Lightweight construction is of particular significance for Germany’s industry to compete on a global scale and, hence, for “Made in Germany”; as a central core technology it strengthens our international top position,” confirms Dr. Elmar Witten, General Manager of AVK and the trade association Composites Germany, one of the initiators of the position paper “Deutschland muss Leitanbieter für den Leichtbau werden” (Germany must become the Lead Supplier for Lightweight Construction).
New processing methods are in high demand
Considered an especially promising processing method is Resin Transfer Molding (RTM) because already today it achieves short cycle times of just a few minutes. “The mass production of automobiles still primarily relies on GRP at present. For one thing, CFP parts are still too expensive and, for another, there are no suitable processing methods available yet that would live up to the high standardisation requirements and production speeds in automotive manufacturing,” said analysts in a study conducted by market research institute Ceresana in 2017.The VDI Centre for Resource Efficiency also sees enormous growth potential for composites in the transport sector in its report “Bestandsaufnahme Leichtbau in Deutschland” (Snapshot of Lightweight Construction in Germany) published in 2015, that analysed hitherto unpublished market studies. Here analysts expect an average annual growth of 7% to 8% in the transport sector and forecast the global market to reach some EUR 140 billion by 2020. The authors identified automotive manufacturing and commercial vehicles, in particular, as the main drivers.
One example of a possible successful cooperation between an automotive manufacturer and a composites producer comes care of Composites Europe exhibitor SGL Technologies. During the 8-year cooperation with BMW, SGL’s lightweight construction solutions have been instrumental to the success of the i3 and i8 models. Looking back on another successful collaboration begun in 2015 are DowAksa and Ford. Here the aim is to accelerate the development of CFP applications for future series and, hence, for largescale production. The partnership between Henkel and Benteler-SGL has resulted in the series launch of a composite transversal leaf spring in not just one but several Volvo models. The transversal leaf spring integrated into the rear axle brings about a weight reduction of 4.5 kg compared to conventional steel coil springs, which reduces fuel consumption as well as CO2 emissions and creates additional space in the trunk.