Plastics Recycling: a Second Life for a Valuable Raw Material
As a raw material, plastic can make a valuable contribution to environmental protection and to the energy revolution. Key to both is the efficient recycling of plastics. For this reason, plastics recycling is the focus of comprehensive development projects at Coperion. The company will show the results of these projects at K 2022 in its pavilion on the open-air fairgrounds (CE09) within the VDMA Circular Economy Forum. There, Coperion will present its combined process solutions and technologies for the economical recycling of various plastics while achieving the highest levels of product quality. At the center will be a system built around a ZSK 58 Mc18 twin screw extruder configured for manufacturing high-quality PET using recycled materials.For feeding voluminous flakes and fibers (PET and other plastics) efficiently into the ZSK twin screw extruder, Coperion will show the SWB-300 Smart Weigh Belt Feeder with a S100 single screw pre-feeder, as well as the new ZS-B 70 MEGAfeed side feeder. The SWB is an extremely reliable gravimetric feeder from Coperion K-Tron that can process large volumes of bulk materials with a wide variety of flow properties at very high accuracy. Using the innovative, newly developed Coperion ZS-B MEGAfeed, plastic recyclate with a bulk density under 200 kg/m³, long considered intake-limited and thus not worth recycling, can be reliably fed in large quantities into smallers of Coperion’s ZSK twin screw extruders and be concurrently recycled and compounded.
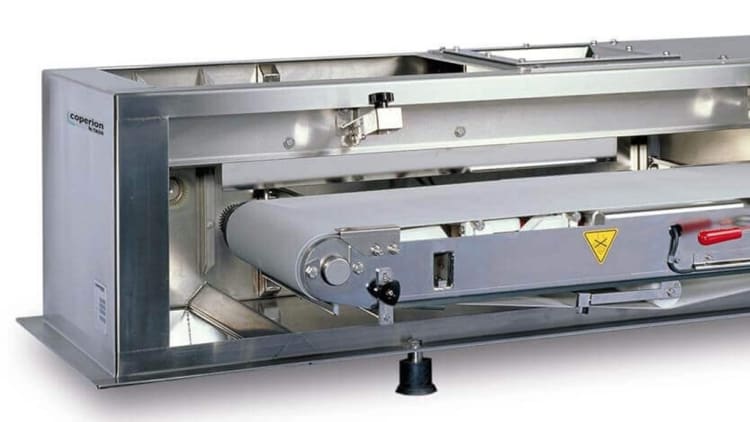
The SWB-300 weight belt feeder from Coperion K-Tron is an extremely reliable gravimetric feeder offering high accuracy and efficient process control.
Melting, intensive devolatilization, and complete homogenization take place in the process section of the ZSK 58 Mc18, before the material stream is transferred via a gear pump and filter with an automatic screen pack changer to an underwater pelletizer for pellet production. Finally, the pellets are condensed in the SSP (Solid State Polycondensation) reactor and can then be processed again into bottles, fibers, or films. The high quality of recycled PET manufactured using this innovative Coperion process was approved by the U.S. Food and Drug Administration (FDA) for direct contact with food (letter of non-objection).
Conventional technologies for recycling PET require pre-drying and crystallization of flakes and fibers before they can be re-processed. Using Coperion's technological process solution, PET recyclate can be introduced directly into the ZSK extruder. Recyclers profit particularly from the very high end product quality. Thanks to the ZSK’s very good devolatilization properties, volatile components such as monomers, oligomers and water are reliably removed. Savings in operating and logistics costs as well as reduced energy consumption are further advantages of Coperion systems for recycling PET.
If the plastic pellets produced create undesirable odors, these can be reliably removed using deodorization equipment from Coperion. In order to optimize such deodorizing equipment’s specification and to individually determine its operational parameters, Coperion now provides onsite tests using a mobile unit for reducing plastic pellet and recyclate odor at customers’ production facilities. Using this solution with freshly produced product and under actual production conditions, the possibilities for reducing recyclate odor can be thoroughly investigated, and system parameters to achieve desired product quality can be defined on location. Coperion will exhibit this mobile deodorization unit in its Recycling Pavilion (CE09).
Marina Matta, Team Leader of Process Technology Engineering Plastics at Coperion, said: “Plastics recycling is one of the core topics that we are emphatically promoting in order to better support the plastics industry on its path to a circular economy. We are very proud of our newly developed technologies and processes that achieve first-class product quality and make plastics recycling significantly more efficient. The innovative ZS-B MEGAfeed makes recycling of some plastic film and flake even possible in the first place. With our new Recycling Innovation Center, we will soon have the optimal environment for developing further technologies and working together with our customers to optimize recycling processes. We’re awaiting completion of the Recycling Innovation Center with excitement and great anticipation.”