“Our decades of competence kicked in while we were developing the VacuFil. What Oerlikon Barmag brings to the table as a technological leader in the field of filament yarn spinning systems, BBE complements with considerable knowhow in the area of extrusion and filtration and in systems construction and engineering!”, states Dr. Klaus Schäfer, CEO of BBE.
BBE is the exclusive supplier of extrusion filter technology for various manmade fiber industry polymers, particularly polyester, for its parent companies. As a result of its association with the Brückner and Oerlikon Textile groups, BBE is always aware of the requirements of the further-processing industry in terms of granulate and melt made from recycled polyester. It is also, and particularly, for this reason that the further development of postconsumer PET material and post-production PET material is of special interest to BBE’s parent companies and the reason for them bundling their recycling know-how to form the BB Engineering joint venture.
BBE is located at the same site in Remscheid as Oerlikon Barmag. When it comes to the downstream processes with the VarioFil spinning system – the basis for spinning high-end manmade POY and FDY fiber filaments for textile and industrial applications that has been tried-and-tested for decades now –BBE is already an established manufacturer of compact and flexible systems for the manmade fiber industry. VarioFil R spinning systems have been used for converting PET regranulates and – directly – PET flakes into POY/DTY for both textile and carpet applications. And spin-dyed products made from PET recycled granulates are also being produced using VarioFil systems. The development, construction and assembly of VacuFil and VarioFil units are carried out exclusively in Remscheid, very much in line with the company’s tried-and-tested ‘Made in Germany’ machine construction philosophy.
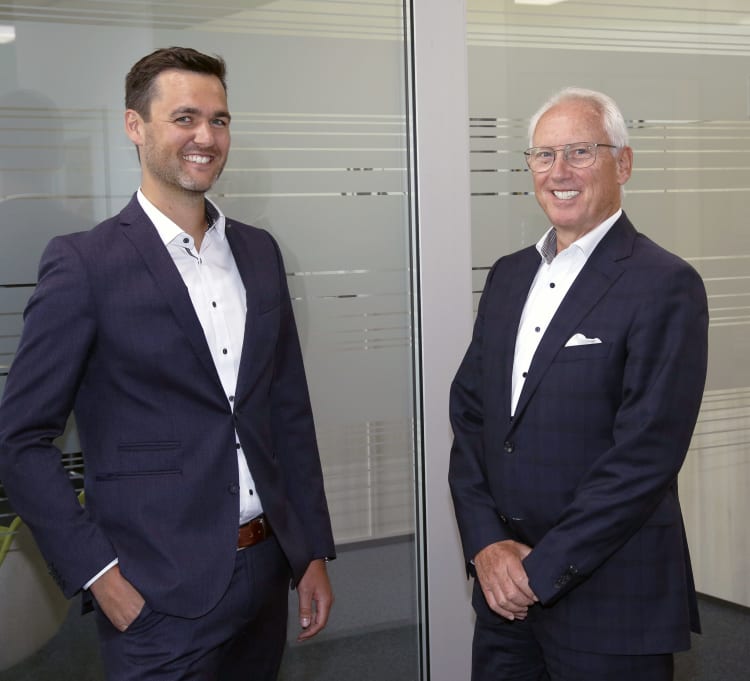
Matthias Schmitz, VacuFil Product Manager, and Dr. Klaus Schäfer, Managing Director
VacuFil premiered at the ITMA 2019 in Barcelona, garnering considerable attention at the trade fair. Since then, numerous tests have been conducted on the pilot system at the Remscheid site using authentic waste material supplied by various customers. The polyester recycled using the VacuFil has been successfully spun into POY and FDY. Various target viscosities and starting materials are not a problem for the VacuFil thanks to the innovative key component, the Visco+ vacuum filter. A reactor is not required. The VacuFil unites gentle large-scale filtration and swift intrinsic viscosity build-up for consistently-outstanding melt quality. The attached vacuum unit, which is automatically regulated between 1 and 30 mbar, removes volatile contamination, ensures a controlled IV increase and additionally achieves an ideal melt homogeneity, which is vital for the downstream spinningperformance. Comprising an inline viscosity measuring unit connected to the vacuum system, the IV can be continuously and reliably adjusted. Hence, producers are able to generate the specific kind of recycled polyester they require for their application. The excellent degasification performance additionally relieves energy-intensive pre-drying.
With their modular structure and a performance spectrum of between 300 kg/h and maximum 3,000 kg/h, VacuFil systems open up various possibilities for processing polyester waste. Bottle flakes, agglomerated spinning waste or a mixture of both can be processed into high-quality PET granulate or fed directly into downstream processes (i.e. the spinning plant). The entire recycling process is controlled and monitored by Oerlikon Barmag’s GUIDE system, guaranteeing the accustomed reliability. With an optional 3DD mixer, the market-proven mixing technology manufactured by BBE, producers can not only add additives to the melt, they can also easily change rPET ratios in the main melt from between 5 and 50 percent stream in order to comply with legal standards.
Customer requirements can be optimally catered for with various system configurations. “The close collaboration between the future operators of the system and our experts ensures that projects are successful. Tests carried out using authentic raw material supplied by customers in our small-scale production system guarantee a sophisticated process that complies with the mentioned requirements. With our process visualization system, customers always have a close eye on the broad operating window and the optimum operating point. And if this is occasionally not the case, our software supplies useful process optimization information. This saves costs and increases productivity!”, explains Matthias Schmitz, VacuFil Product Manager.