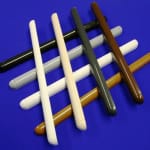
Recent developments in colour concentrate technology enable processors to add colour in-house and benefit from increased manufacturing flexibility, tighter purchasing, reduced inventory and closer quality control.
Traditionally self colouring PVCu has never been as successful as colouring commodity polymers, but there is no reason for it not to be.
In-house colouring offers reduced costs by facilitating the purchase of natural polymer from a supplier of choice and reducing stock holdings of coloured compounds.
Common methods of colouring PVCu include:
- Dye packs – a blend of pigment and dyes
- Liquid colours – a dispersion of colourants in a liquid carrier
- Wax dispersions – a solid dispersion of colourants in a wax
- Masterbatches - colourants compounded into a universal or polymer specific carrier resin
Health and safety – dusty powder pigments require the use of personal protection equipment. Special plant such as dosers, pumps etc., might be needed to introduce the colourants to the polymer. Quality control may need to be enhanced to ensure the accurate addition of colourants. This could mean extra training or employing qualified staff or investing in test equipment such as spectrophotometers. Higher levels of cleanliness may be necessary along with dedicated storage facilities with temperature and humidity control, regular agitation etc.
There will also be additional demands on the process to homogenise the colourants into the polymer.
Finally, ease of use which takes into account the process, the application, colouring criteria and amount of colourant required to achieve the desired colour and opacity.
Formulation of concentrates
Formulating a colour concentrate for PVCu is not as simple as with other polymers. Although based on a PVC resin, unplasticised PVC compound formulations are complex and contain many ingredients: stabilisers, fillers, impact modifiers, processing aids, and lubricants are commonly used. The choice of these can vary immensely; even the level of compounding depends upon the application.Many concentrates employ one ingredient as the carrier, selected for its ability to accommodate large amounts of pigment without adversely affecting processing or performance when added to the host polymer. Side effects can be undesirable, especially if the colourant carrier is also a lubricant in the PVCu.
With liquid and wax systems care has to be taken with carrier choice to avoid plate-out, screw slip and other melt rheology problems. Some liquid carriers plasticise PVC, introducing a plasticiser to a material selected for its lack of plasticisers!
Masterbatches are equally complex. Universals generally work well in PVCp while grades created for use in PVCu can be troublesome when used at high loadings. Universal types based on high VA content EVA are fairly successful, but these too can have a plasticising effect. They are also unsuitable carriers for dyestuffs.
Assuming the colour is suitable the processor then has to consider the effect of the colour concentrate on the melt rheology of the compound as well as any evidence of incompatibility - appearing as lamination in the finished product.