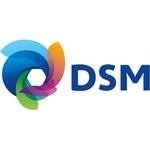
DSM Engineering Plastics announces that its global headquarters have moved to Singapore. The Company, which has development, sales and manufacturing facilities located in The Netherlands, USA, Japan, China, Taiwan, India, Belgium and Russia has moved a number of its key functions to Asia in order to underline its commitment to the Asian market which is expected to represent the major share of the company’s growth in the coming years.
According to Roelof Westerbeek, President DSM Engineering Plastics, the move - which was pre-announced in 2010 – is making good progress and will be completed in 2012: “This is a significant step as it puts us right at the heart of the fast-growing Asian marketplace. It will help DSM Engineering Plastics to quicker anticipate the needs of our customers, both regionally and globally. In addition, it underlines the high importance that DSM puts on high growth economies as one of the key growth drivers.”
At present, DSM Engineering Plastics has the following key facilities in place in Asia: manufacturing facilities in China, Japan, India and Taiwan – as well as Research facilities in China. The Company also has the intention to establish research capabilities in Japan and India. Combined, these facilities provide an excellent backbone for the company’s extensive market development and sales support activities throughout Asia.
Rein Borggreve, Global R&D Director: “As a global supplier of high-performance engineering thermoplastic solutions, we want to ensure that our world-class product portfolio and technical support are available throughout Asia – for both local and global players.” Around the world, DSM has a team of specialists ready to offer support, provide answers and help with design and engineering, as well as provide specific product or application testing.
Following the move, DSM remains committed to its world-wide customer base, many of whom also have a large presence in Asia Pacific. Roelof Westerbeek: “Throughout the world, in Asia, Europe and the Americas, DSM offers an industry-leading portfolio of sustainable thermoplastic technologies. Our leadership in Eco+ solutions is demonstrated by a complete portfolio of halogen-free engineering plastics, developed for a wide range of high-performance applications. This has been further strengthened by the successful launch of new innovations such as Stanyl ForTii, a revolutionary new breakthrough high temperature polyamide for demanding applications in the electronics, lighting, automotive, white goods, industrial and aerospace industries.”
DSM strives to further improve the environmental performance of its products. The most innovative developments in this field are new bio-based polymers and bio-based building blocks. DSM is already making good progress with EcoPaXX, the best-performing green polymer available, with a zero carbon footprint (cradle to gate).
Recently, DSM introduced Arnitel Eco, a unique material creating more value with lower environmental impact. With up to 50% made of renewable resources, this thermoplastic elastomer delivers a lower carbon footprint, a lower impact on climate change and improved durability.
DSM is passionate about playing a leading role in the development of more sustainable solutions with reduced environmental impact. Recognizing the growing interest in recycling with the ultimate goal of achieving closed-loop systems, DSM has adopted the Cradle to Cradle concept as part of its sustainability strategy. DSM is also actively replacing hazardous materials, particularly by introducing halogen-free alternatives, such as Arnitel XG (used in consumer electronics cables), and Arnite XG (used in electrical insulation in white goods). Another recent example is Stanyl ForTii (especially in electronic connectors), a new breakthrough high-temperature polyamide with halogen-free flame retardant grades.