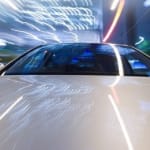
DSM's ForTii offers a class-leading combination of processability and high mechanical performance over a wide temperature range. The portfolio already includes grades that offer numerous advantages over die-cast aluminium and zinc, and the range will be further expanded over the course of this year.
ForTii retains its high stiffness and strength, even in high-temperature, high-humidity environments. It also exhibits outstanding dimensional stability over a wide temperature range and keeps its impact strength at low temperatures. This makes it very suitable for the use in highly loaded structural parts, where normally die cast metals are considered.
Significant weight savings - sometimes by as much as 50% or even more - can be achieved by injection molding parts designed specifically for ForTii. Total part costs can also be reduced, often by 20-30%.
As an example of what can be achieved with ForTii, DSM highlights the housing of a newly redesigned compact air compressor used in car repair kits to fix flat tires, as well as for various leisure activities. The pump is made by Chinese company Guan Xiang, a leading producer of portable air compressors. By injection molding the housing in ForTii instead of die-casting it in zinc, Guan Xian has reduced the weight of the air pump by more than 50%. In addition, the company was able to significantly reduce its production costs, as ForTii enabled extra functional integration and eliminated secondary assembly operations associated with zinc die-cast part.
A single component in ForTii replaced several die-cast zinc components in the air pump. The pump has to show a very high level of reliability in a wide range of operating conditions; for example, it has to be able to operate in ambient temperatures as low as -20°C while the internal operating temperature can reach over 200°C. Tests on the new design have in fact shown that it operates reliably at temperatures as low as -30°C and as high as 250°C without failure.
DSM worked very closely with Guan Xiang to ensure that ForTii met all the customer's performance and manufacturing criteria. "The performance of ForTii and the excellent engineering support at all stages of the development process from DSM allowed us to realize this important new component in the pump, the heart of our tire repair kit," says Mr. Xie Jun, purchasing supervisor from Guan Xiang.
"The outstanding combination of dimensional stability and mechanical strength at low and high temperatures in dry and humid conditions allows customers to consider using ForTii in applications they have not considered possible in our plastics until now," says Ralf Ponicki, Global Program Manager Die Cast Replacement at DSM. "ForTii enables complex part geometries that cannot be achieved with die casting: parts can be made with integral threads and snap fits, and if housings need to be made in more than one part, they can be welded rather than screwed together for better seals."
"Engineering plastics from DSM have proven themselves time and again to provide high levels of reliability in highly loaded applications. With the expansion of our total portfolio of high performance thermoplastics, which now includes polyamide 46 (Stanyl), polyamide 410 (EcoPaXX) and PPS (Xytron), as well as the rapidly expanding PPA (ForTii range), we will be able to strengthen our position as an important partner for customers across industries looking for die cast replacements."
DSM continues to search for even better solutions, with higher mechanical performance, even more suitable for die-cast metal replacement, and which will help to meet future industry requirements, such as reduction of CO2 emissions from automobiles and the reduction of energy consumption in industrial & consumer applications.