
Efficiency and electromagnetic protection are becoming increasingly crucial in the plastics industry. That is why, Delta Tecnic a company specialized in the manufacture of masterbatch for the plastics and cable industry, takes a step forward with the launch of its own line of metallic fiber masterbatches. This technology is designed to improve the conductivity of plastics and offer advanced solutions in electromagnetic shielding (EMI Shielding), a key challenge in sectors such as automotive, electronics and telecommunications.
Traditionally, the conductivity of plastics has been based on carbon technology, which limits color options and restricts conductivity and electromagnetic shielding levels due to the maximum absorption capacity of polymers. Delta Tecnic presents an alternative: the incorporation of metallic fibers into plastic composites. This development makes it possible to create conductive plastics that not only offer higher electromagnetic efficiency, but can also be manufactured in a wide range of colors, something previously unthinkable with carbon-based solutions.
Delta Tecnic’s new metallic fiber masterbatch, composed of 75% metallic fibers and 25% polymer, is dosed directly in the injection or compounding processes. This mixture allows the customer, usually manufacturers of technical compounds, to produce compounds for conductive plastic parts with freedom of color and allowing the substitution of metal parts for plastic parts, while maintaining the conductive and electromagnetic shielding properties.
Key applications: automotive, PVC and more
One of the most prominent applications of this technology is electromagnetic shielding in automotive parts. With the increasing adoption of electric vehicles, where high-voltage cables generate electromagnetic fields that can interfere with other electronic systems, plastic parts that previously did not require shielding now need efficient shielding. Delta Tecnic’s metal fiber masterbatch allows these parts to be manufactured more economically and light weight, key features in the automotive industry.
In addition, this breakthrough also has applications in the production of conductive PVC flooring, used in environments where it is essential to dissipate electrostatic energy, such as in hospitals. PVC floors made with this masterbatch allow the transmission of electrical energy without accumulating charge, reducing the risk of static discharges and increasing safety in critical installations.
Another interesting field of application is the production of conductive wheels, such as those used in industrial trolleys used for the movement of raw materials in industry and factories. These wheels, being conductive, prevent the accumulation of static charge that could damage equipment or even represent a shock hazard.
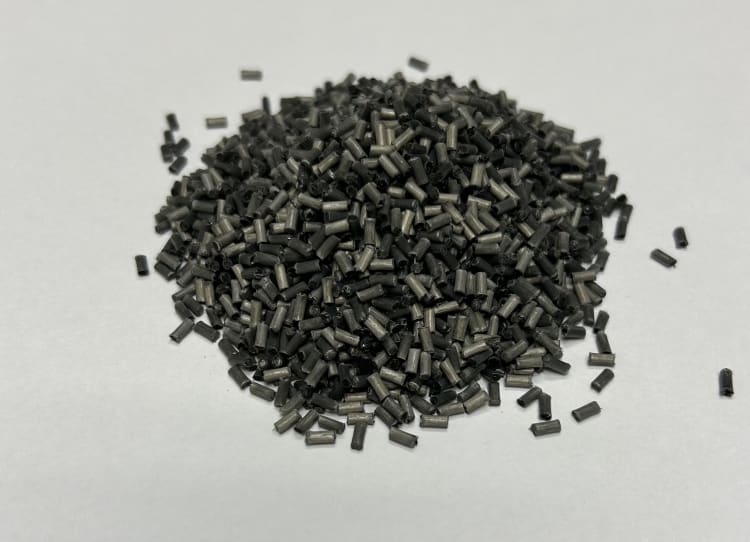
An advanced solution for electromagnetic shielding
The metallic fibers within the plastic matrix help to create a “Faraday cage”, which acts as a barrier to electromagnetic interference generated by magnetic fields. This type of solution is vital in an increasingly connected environment, where data transmission and security of electronic systems are critical and the reduction or elimination of all types of interference is vital.
“Thanks to our constant commitment to innovation, Delta Tecnic has developed a technology that improves the efficiency and electromagnetic properties of plastics, and also facilitates the production of lighter, more colorful and better performing parts.”, highlights Manuel Miret, Area Manager & New Product Developer at Delta Tecnic. “Metallic fibers offer manufacturers a powerful tool to adapt their products to the demands of a market that requires more efficient, safer and more economical solutions.”, states.