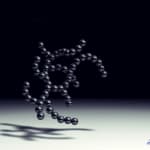
In critical applications where static electricity poses risks to the safety and operation of sensitive equipment, it's essential for floors to achieve a certain level of conductivity. With deep technical knowledge and decades of industry experience, Delta Tecnic, a leading manufacturer of PVC masterbatches, steps in to offer advanced solutions ranging from static energy dissipation to electrical semiconductivity.
The company has historically been a pioneer in manufacturing PVC materials with dissipative and semiconductive properties using carbon black. This is because a significant portion of the market relies on PVC polymer, widely used in various applications including flooring, flexible hoses, and shoe soles. PVC is a versatile material employed in the production of flexible flooring for a wide range of environments such as sports facilities, hospitals, and high-traffic areas.
In these settings, ensuring that floors are dissipative is crucial to prevent static buildup, which can pose risks to the safety and operation of sensitive equipment, such as in operating rooms or chip manufacturing facilities. In this regard, Delta Tecnic specializes in manufacturing compounds specifically designed to meet these requirements, offering proven and reliable technological solutions to mitigate static-related risks in critical environments.
It's important to note that due to the high amounts of dopant required to achieve desired conductive properties in PVC materials, Delta Tecnic does not employ the typical masterbatch process. Instead, they manufacture compounds - homogeneous blends of polymer and additives—designed to impart the necessary electrical properties to the final product.
Delta Tecnic's technical expertise and capability to effectively disperse additives within the polymeric matrix are fundamental to their success in this field. Proper dispersion of conductive additives is crucial to ensuring optimal performance of the final material. Delta Tecnic utilizes specialized machinery and a team of dispersion experts to ensure the quality and consistency of their custom conductive compounds.
How does Delta Tecnic provide conductive properties to PVC materials?
In detail, the company employs a variety of carbon-based additives to impart conductive properties to plastic materials. The molecular structure of these carbon derivatives is crucial: their length allows electrons to move along them, creating a network of carbon atoms within the plastic material.
There are three main types of carbon-based dopant additives used by Delta Tecnic: carbon black, carbon nanotubes, and graphene. Each of these additives has unique characteristics and structures. Carbon black consists of finely divided carbon particles that form a dispersed network within the plastic. Carbon nanotubes have a tube-like structure, whereas graphene has a two-dimensional sheet structure.
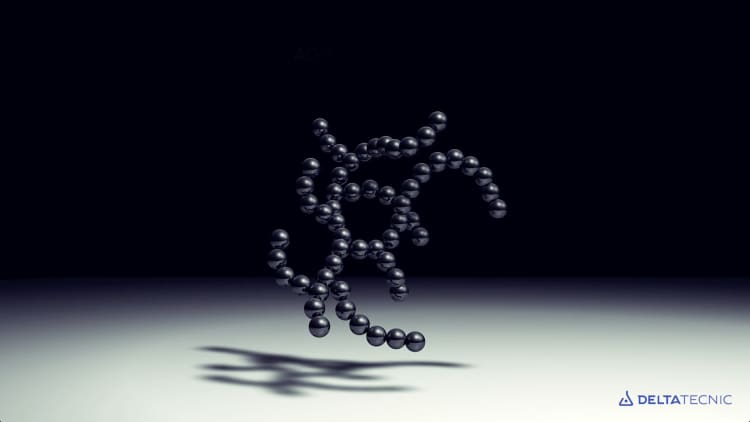
These dopant additives have different effects on the electrical properties of the plastic material. For instance, conductive carbon blacks require a higher amount of additive within the polymeric mass to achieve the desired conductivity, typically ranging between 15% and 30% of the total plastic weight. In contrast, carbon nanotubes require a lower concentration, usually between 3% and 7%, while graphene can provide even higher conductivities with concentrations ranging from 2% to 5%.
It's important to note that the amount of additive used affects other properties of the plastic, such as impact resistance and aesthetics. The more additive added, the greater the impact on these properties. This can be crucial in the manufacturing of final parts that require a certain level of mechanical strength or are exposed to specific environmental conditions. Therefore, striking the right balance between electrical conductivity and other material properties is essential in the product development process.
Metallic fibers: a new approach to dissipating and conducting electrical energy.
Very recently, Delta Tecnic has begun manufacturing masterbatches that enable the passage of electrical energy through very fine-diameter metallic fibers. These fibers are produced in a masterbatch form that can be applied during injection molding or even in the manufacturing of compounds for subsequent transformation.
The ability to conduct electrical current with these metallic fibers opens a new dimension in the production of conductive compounds, without the limitation of the black color typically imposed by traditional carbon-based dopants.
These metallic fibers, integrated into plastic parts, can achieve highly interesting conductivity values and offer the potential for significant electromagnetic shielding. This comes at a time when reducing the weight of parts and simplifying their manufacturing process is imperative.