PCR (post consumer resins), another step forward in rPET
The recycling of the resins that make up the container for food grade use is a primary objective of the research and development promoted by leading technology suppliers like SACMI, which, for years now, has been offering the possibility of processing up to 100% rPET, and up to 50% recycled PET in the form of flakes, on its standard range of preform presses (IPS).
Being introduced on the market today is an innovation that allows this percentage to be increased up to 70-75%. This innovation also redesigns the entire process for optimal handling of flake and granule mixtures, with no need for two separate processing hoppers, for a potentially ground-breaking innovation in terms of efficiency and user-friendliness, which will facilitate the market switch to a chain complete with food-grade PET recycling.
And that’s not all: SACMI is currently preparing to further expand its recycling approach for food grade use products to include the entire cap-preform system, and is simultaneously continuing with its research and prototyping of new biocompatible polymers, such as cellulose-based fibres and blends.
Once again in this case, it is the unsurpassed expertise and know-how of its Laboratory, together with its daily support for its customers around the world, that allow SACMI to continue driving innovation, above all sustainable innovation, in this sector.
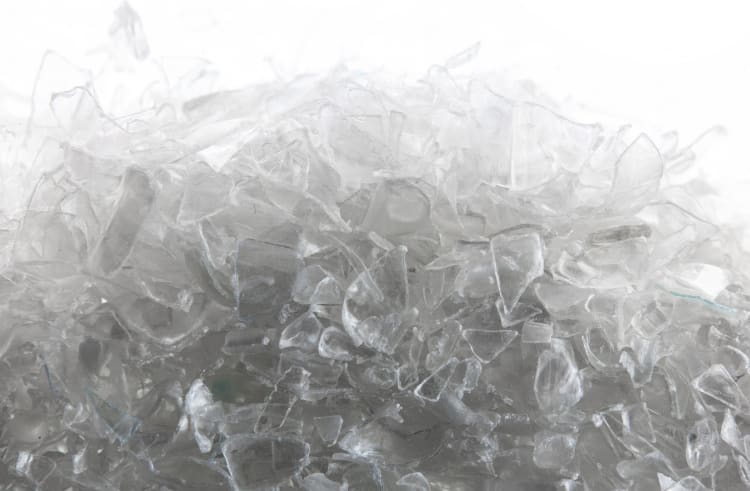
The new CM-Flow extruder & Computer Vision
In general, the availability of advanced features and controls on the machines ensures their increased availability and efficiency, thus reducing waste. The inherent superiority of the compression process, which operates at lower temperatures than the injection process, fosters progress in this direction, also thanks to the additional innovations that SACMI has made available on its CCM press range.
These include the new CM-Flow extruder, which is available on the new CCMs, but can also be installed on several existing machines. This feature saves energy by improving the quality of the extrusion process, with a reduction in the risk of black spots by up to 50%, as demonstrated by customers who have opted for this solution. This is an additional possibility, and does not replace, the 'Smart Pack' service, which is available on all the new-generation presses.
Finally, with regard to the ‘vision’ systems, SACMI offers several families of solutions based on artificial intelligence algorithms for performing quality controls on the cap, the cut, and the preform. The advantage of these systems is that they provide a basis for developing the quality control concept in the direction of proactive process monitoring, thanks to the real-time availability of useful data and information, which can be used to detect production deviations in advance and to predict the necessary actions to be taken.
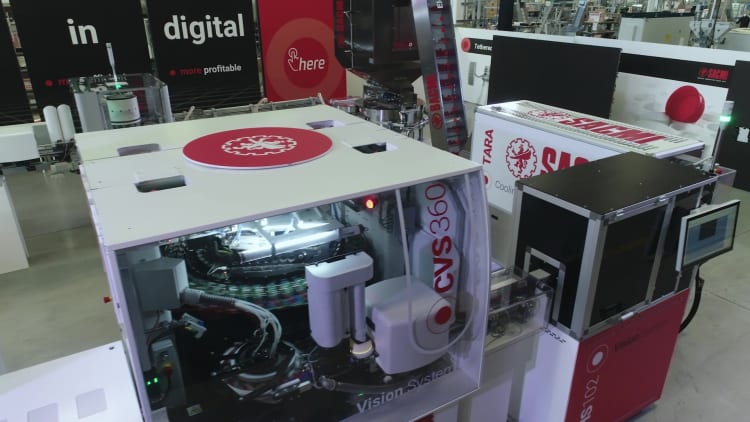
Visit us at Drinktec 2022! (HALL B5 booth 302/304/101)