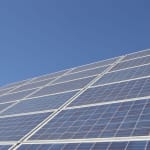
It is 2022 and we are at the K trade fair in Germany. What visitors to the Wittmann booth in Hall 12 are experiencing is bordering on a revolution. An injection molding production cell is making electronic parts from a flame-retardant polyamide and boasts eye-catching solar panels - this is a conceptual study presented by Wittmann in collaboration with a customer. Supported by the appropriate infrastructure, the injection molding machine and the robot are being powered directly by solar energy via a DC link. The two partner companies have jointly filed a patent for this development.
Fast-forward a year and, at Fakuma 2023, Wittmann is again presenting a production cell powered directly by direct current (DC) obtained from solar energy. This is no longer a conceptual study, but a production-ready solution that includes solar power storage. Wittmann has joined forces with another partner company with the aim of industrializing and marketing DC injection molding technology. The partner company, which has been operating under the name inesco AG since autumn 2024, has been working for more than ten years on the question of how renewable energy can be used sensibly and stored efficiently on a large scale.
This presentation at Fakuma 2023 sets the ball rolling. The injection molding industry is now very interested in the direct use of solar power via DC grids. As a result, Wittmann and inesco are currently evaluating and processing a number of inquiries on specific projects. The first DC-capable injection molding machines have been sold.
Wittmann has pioneered DC technology in the injection molding industry. It is the first supplier to offer injection molding companies machines and production cells that can use solar energy sourced directly from a DC grid.
Focus on security of supply
Like other types of renewable energy, such as that generated in wind farms and biogas plants, solar power is direct current (DC). However, national power grids use alternating current (AC). Before alternative types of power can be used, they need to be converted into AC. DC is converted into AC so that it can be transported and distributed - and in some cases the AC is transformed back into DC at the consumer, many of which work with DC. The converters employed are primarily frequency inverters used for infinitely-variable control over the speed of electric motors, which account for 70 % of power consumption in industrial environments. Other examples of DC consumers are computers, televisions, LED lamps and electric vehicles.
In industrial production as well as in everyday life, DC is constantly being converted into AC and vice versa. With each transformation, there is a loss of energy, in the order of 2 to 4 %. This lowers the energy efficiency of the applications. It was this consideration that prompted the idea of making direct current directly usable via decentralized DC networks, called DC microgrids, without converting it first into alternating current.
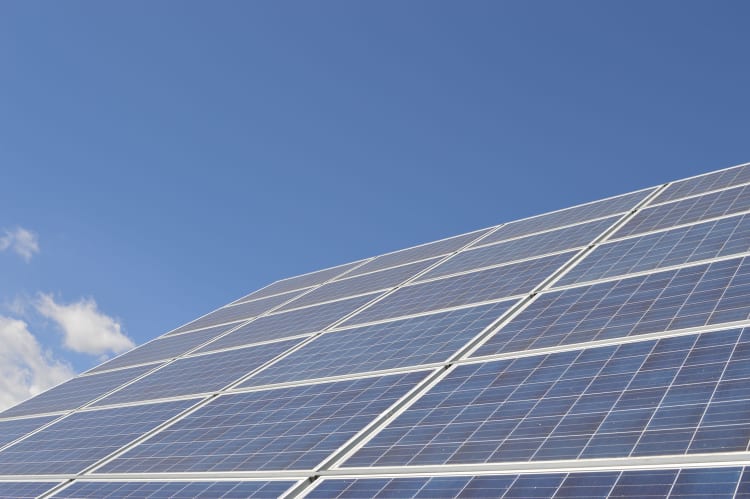
from the electricity market - especially since the use of renew-able energy also contributes to the attainment of sustainability goals.
Aside from energy savings and the associated smaller carbon footprint, there are other motivations for looking into the possibilities afforded by DC technology. First and foremost is security of supply. Rising electricity consumption due, among other things, to the proliferation of electric vehicles and heat pumps, as well as advancing electrification of industrial production are placing ever-greater loads on existing power grids, which are often not expanding in line with developments. This situation is being exacerbated by the rapid rise in feed-in solar power, which is putting additional strain on the grids and making them more unstable. Experts say that even countries which have very good electricity supplies, such as Germany and Austria, could increasingly experience grid failures and restrictions on consumption in the future. Direct-current grids could therefore evolve into an important building block for ensuring security of supply and climate neutrality. One argument supporting this is that direct current is easy to store in batteries, providing an efficient way to cover expensive power peaks.
Another is greater resource efficiency when it comes to the expansion of power grids. Thanks to modern technology, three-wire DC grids require substantially less copper conductor material than five-wire AC grids, as well as fewer electronic parts: There are no rectifiers at all in the equipment.
Solar Storage Batteries Keep Output Constant
What does the direct use of solar power in injection molding operations look like in practice? Wittmann's solution is based on three components: A Wittmann injection molding machine or production cell modified to use DC technology, inesco’s DC network “DConnect”, and a sodistore max storage battery based on natrium salt. The salt battery was developed specifically for sustainable use by industrial companies.
The DConnect forms the backbone of the DC power supply during operation. It is a self-regulating DC microgrid into which DC producers and DC consumers can be easily integrated and interconnected. DConnect works without an external controller and does not require an internet connection. This means that the system is securely protected against cybercrime.