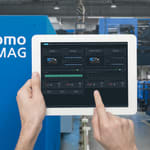
Sumitomo (SHI) Demag will demonstrate on eight exhibits how, advanced digital tools like myAssist and activeMeltControl can help to increase production efficiency, improve component quality and reduce machine downtime, when combined with a unified communication platform.
Having access to real-time data not only transforms service models and increases machine uptime, it also leads to better and faster business decisions. At Fakuma 2024 booth B1-1105, Sumitomo (SHI) Demag will demonstrate to visitors how digital features like myAssist, automation, the company’s active modules and OPC-UA connectivity can help manufacturers optimise productivity and virtually eliminate machine downtime.
Providing greater processing transparency to help run machines at maximum efficiency, Sumitomo (SHI) Demag will unveil its recent advances in its myAssist software and how further optimisations offer processors even deeper data insights. Summarised by the company as the ‘ultimate digital process companion’, these newest upgrades include easy-to-read dashboards, consumption data and KPIs, all defined by the end user. The ability to use one interface to connect and oversee digital data across multiple machines in a single production facility is also available.
This level of high data transparency makes it possible to spot deviations, aggregate data captured from all OPC-UA filtered sources and react to changes in production processes at the earliest stage. Live data can be compared against any historical data. This comparison can be made on the basis of different time intervals, such as different production hours, weeks or even complete production orders.
“Having the ability to merge data from multiple sources allows for complete digital mapping of all production and environmental factors, including historical data,” notes Product Manager of Digital Solutions, Dr. Thomas Schilling. Adding Human Virtual Interface (HVI) and an Expertise module also enables users to put data findings into context by adding labels and more detailed annotations. In turn, this allows manufacturers to gain the greatest possible value from their data. This option will be available on all new IntElect machines from 1 January, 2025.

Creating connections and standard interfaces
Data holds intrinsic value with the ability to optimise productivity and increase profitability, but only if it is collected and handled correctly. With the momentum and move towards smart manufacturing and Open Platform Communications Unified Architecture (OPC-UA) interoperability continuing at pace, Sumitomo (SHI) Demag will explain how the company is facilitating scalable and extendible communication between injection moulding machines, periphery equipment and automation.
One of the biggest obstacles to machine learning and digital factories of the future is not having a standard interface, asserts Thomas Schilling. “For seamless communication to take place across machinery assets, all of the elements, including sensors and processing data, needs to talk to one another in the same language. That’s what OPC-UA seeks to accomplish - a universally compatible digital interface. Which ultimately delivers time savings and productivity benefits to injection moulders,” adds the digital expert.