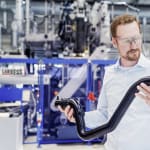
According to studies conducted by Lanxess, around 80 percent of newly registered vehicles in 2035 will still have a combustion engine – in the form of either a mild-hybrid engine, plug-in hybrid engine or pure combustion engine. The trend will shift toward turbocharged engines because they are more efficient and more eco-friendly. The charge air duct in these engines must be capable of withstanding increasingly higher temperatures due to the smaller installation spaces, rising engine power and new engine designs. This is why Lanxess has developed Durethan AKV320ZXTS2 (currently available as Durethan TP202-048), a blow-moldable polyamide 66 that, thanks to its thermal durability of up to 230 °C, is capable of meeting exceptionally high temperature requirements. The abbreviation XTS stands for “Extreme Temperature Stabilization”. At K 2019, the international trade show for plastics and rubber taking place in Düsseldorf from October 16 to 23, the High Performance Materials business unit will be showcasing this innovative compound.
Smooth inside pipe surfaces
The new compound is a further development of the recently launched Durethan AKV320ZH2.0 and also has a wide processing window for suction blow molding. It is also resistant to pressure changes at high temperatures and produces smooth pipe surfaces with an extremely high-quality surface finish. “Our material does not exhibit any stabilization gaps between 160 °C and 230 °C and still delivers outstanding mechanical performance even at 230 °C,” says Dr. Klaus Küsters, who is responsible for the business development blow molding at Lanxess.
Good strain at break behavior after thermal aging
HPM has extensively investigated the thermal resistance of the new structural material which is toughness-modified and reinforced with 20 percent glass fibers. One typical test is storing the material at different temperatures in hot air. Even after ageing for 3,000 hours at 230 °C, its strain at break is still greater than 2 percent. Therefore, it is the material of choice with engine designs in which charge air cooling is integrated in the air intake manifold. This results in an extremely compact design and, in turn, a high thermal load on the air-ducting parts.
Precise control of wall thicknesses
Like Durethan AKV320ZH2.0, the new polyamide 66 compound has been optimized for a stable production process in a 3D suction blow-molding process. Küsters: “Thanks to its high melt stiffness, the wall thickness of the components can be controlled with an extremely high degree of reproducibility.” Optimizing the material for the suction blow molding process also means that the surface is of high quality even when the parison came into contact with the cool tool during processing.
Source: Lanxess