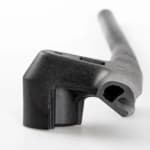
At this year’s JEC World, taking place from 4 to 6 March 2025 in Paris, ENGEL, a global leader in plastics processing technology, is involved in three products that have been selected as finalists for the JEC Innovation Awards. The Austrian injection moulding machine manufacturer, headquartered in Schwertberg, impressively demonstrates the capabilities of its innovative injection moulding technologies for lightweight construction. Among the highlights is the live production of an innovative bicycle handlebar for Canyon Bicycles, manufactured using the fluidmelt process with localised fibre reinforcement on a tie-bar-less ENGEL victory injection moulding machine. Another key exhibit at the ENGEL stand is a revolutionary truck storage compartment flap, which has been named a winner of this year’s JEC Award.
Innovative bicycle handlebar production with a powerful combination of technologies
One of the main attractions at the trade fair is the live production of a newly designed bicycle handlebar, developed in collaboration with Canyon Bicycles. This handlebar is manufactured on a tie-bar-less ENGEL victory 180 injection moulding machine, combining the fluidmelt and organomelt technologies with continuous fibre-reinforced semi-finished products.
With fluidmelt for technical and design flexibility
The fluidmelt process enables the production of hollow structures by injecting water or nitrogen. During the process, the molten core of the component is displaced into an overflow cavity or back into the plasticising unit, creating a hollow space within the part. At JEC World, the process will be demonstrated using gas injection and overflow cavities. Once the cooling phase is complete, the hollow handlebar can be removed from the mould. Thanks to its geometry, this method allows for the production of extremely lightweight structures that also offer high bending and torsional stiffness.
Stability in lightweight construction with organomelt
The use of continuous fibre-reinforced semi-finished products further enhances the mechanical properties of the bicycle handlebar. The components themselves are made of glass fibre-reinforced polyamide 6 to ensure the necessary stiffness and strength. By integrating four UD carbon fibre tapes, which are placed into the mould during the injection moulding process, the part withstands high loads despite its thin-walled and hollow structure. This innovation represents a significant advancement over traditional aluminium and thermoset handlebars, making production in Europe economically viable while also reducing environmental impact.
Technological advantages of the ENGEL victory machine series
The ENGEL victory 180 Wide-Platen machine, showcased in production on the fairground, is an injection moulding machine specifically designed for large and complex components or moulds. Thanks to its tie-bar-less design with a spacious, open mould area, the victory series enables the use of large and intricate moulds within compact machine dimensions. This is a particular advantage for high-volume and demanding applications such as the bicycle handlebar.
With its enlarged platen, the machine offers an additional 100 mm in width compared to standard models. As no higher clamping force is required, manufacturers can avoid investing in a larger machine, thereby saving on floor space and additional energy consumption. This reduces costs and reinforces ENGEL’s commitment to sustainable production processes.
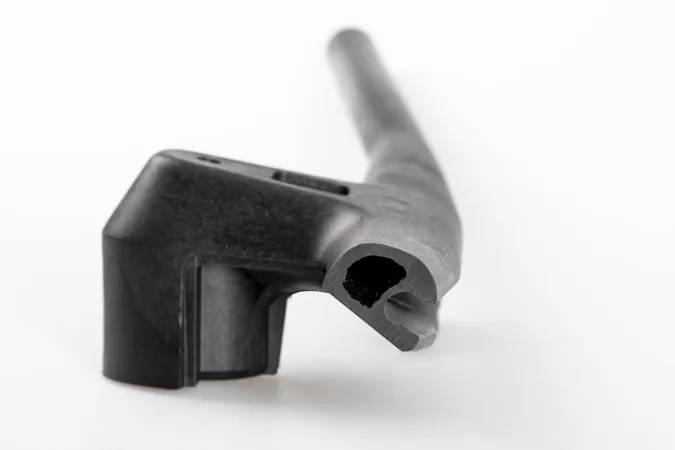
Project partners and their roles:
- Canyon Bicycles, known for its innovations and high design standards in bicycle manufacturing, played a key role in the development of the new handlebar. Their expertise in conceptualisation and functional design ensured that the handlebar meets the high demands of professional cyclists.
- Artefakt Design was responsible for the aesthetic design of the handlebar. They created a design that is not only functional but also visually appealing, seamlessly integrating into the modern look of Canyon bicycles.
- DOMO Chemicals supplied the injection moulding compound and the necessary tapes for production - a crucial contribution to achieving the high performance of the handlebar.
- Plastic Innovation handled the mechanical component design as well as process and structural simulation. Their expertise in this area was instrumental in realising the innovative design.
- Simoldes, as the toolmaker and series producer, contributed its extensive knowledge in mould manufacturing and component production to ensure the high quality and reproducibility of the handlebar manufacturing process.
Winner of the JEC World Innovation Award - a revolutionary storage compartment flap
The second highlight from ENGEL at JEC World is the storage compartment flap for Daimler Trucks, developed by Fraunhofer IMWS. This flap features a visually appealing, full-width edge and a closed, all-around edge, both of which are created in a single step along with the core and structural formation. This places high demands on the precision of the injection moulding process and the machine’s ability to deliver accurate and reliable results, even under high material stress.
This innovative component was manufactured as a sandwich part on an ENGEL injection moulding machine and is the result of the thermoplastic sandwich moulding technology developed at Fraunhofer IMWS. In this process, semi-finished products consisting of a thermoplastic honeycomb core and fibre-reinforced thermoplastic UD tape laminates from project partner ThermHex are thermoformed and can be functionalised via injection moulding in the same process. The continuous and fully automated manufacturing process is designed for high-volume production. This is particularly crucial for the automotive industry, where large production volumes and short cycle times are essential.
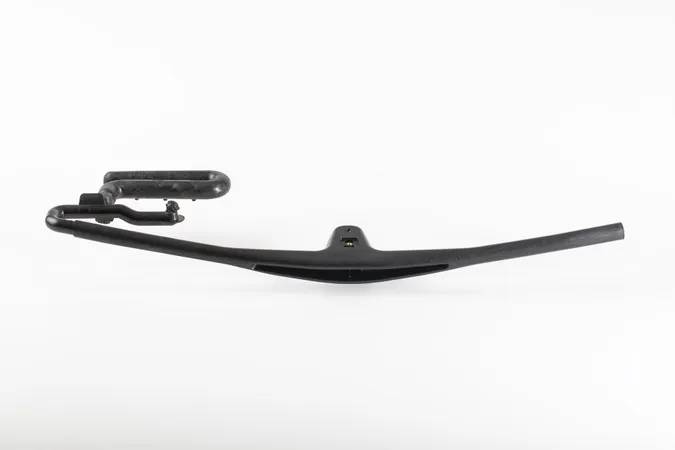
Sustainability through the right lightweight technologies
The storage compartment flap showcased at the trade fair demonstrates how modern lightweight technologies and the right choice of machinery can revolutionise the production of vehicle interior components. Such products enable significant weight reduction while simultaneously enhancing structural integrity. This advanced manufacturing technique helps lower CO₂ emissions and minimise material consumption, making it an environmentally friendly and efficient solution for the automotive industry.
Summary and outlook
ENGEL’s presentations at JEC World highlight the company’s leading role in developing and implementing advanced injection moulding technologies for lightweight construction. Once again, ENGEL is setting new benchmarks in production efficiency and sustainability, opening up new markets for plastic components that have traditionally been made from metal.
Visit us at our booth: Hall 5, Stand L106