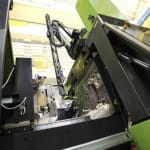
At a very early stage, ENGEL focused on the trend towards networking and digitalising production processes by developing an integrated digitalisation strategy for its own production as well as its customers. "Many of our inject 4.0 products and solutions have already been successfully deployed at customer sites for many years," reports Abdulkadir Topucar, Managing Director of ENGEL Enjeksiyon Makineleri in Istanbul. "At the same time, we are consistently working to develop the range. We are inviting trade fair visitors to experience both established and new products and solutions at our stand, and try them out first hand." In particular, it is the modularity of ENGEL's inject 4.0 approach that makes it extremely easy for plastics processors to start working towards the smart factory step by step. Even individual stand-alone solutions can add great value.
Compensating for process fluctuations before rejects are produced
As integration and automation make injection moulding processes ever more complex, managing and controlling them also needs to be simpler and more intuitive. Self-adapting, intelligent assistance systems make a major contribution towards this objective as they boost process capability and quality without requiring operators to acquire special skills. To clearly demonstrate the way these assistance systems work, ENGEL will be producing inject 4.0 logos at its stand over the four days of the fair using an all-electric and tie-bar-less ENGEL e motion 80 TL injection moulding machine. Fluctuating process conditions will be simulated in the machine's CC300 control unit, giving trade fair visitors the opportunity to track the automatic readjustment by the intelligent assistance systems live on the machine's display. While iQ weight control keeps the injected melt volume consistent throughout the injection moulding process, iQ clamp control determines mould breathing in order to set the correct clamping force for good mould venting. This means that fluctuations in ambient conditions and raw materials are automatically detected and compensated for in a single shot, before rejects can be produced.Efficient, precise and space-saving
The design of the e-motion 80 TL also meets the strictest efficiency and precision requirements. The model range combines the benefits of ENGEL tie-bar-less technology, such as fast tooling processes, efficient automation solutions and compact production cells with all-electric drive technology. Thanks to these qualities, the e motion 80 TL can be used, for example, to manufacture precision parts and premium optical components in the electronics industry.At Plast Eurasia, an integrated e-pic Z robot will remove the parts from the mould. The innovative kinematic system of the pick-and-place robot in the ENGEL product portfolio combines linear movements with a swivel arm, and thus requires minimal space. The swivel arm comprises a tailor-made, lightweight, thermoplastic composite material which also raises energy efficiency and dynamism.