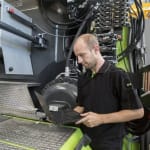
The modularity of ENGEL’s inject 4.0 approach makes it especially easy for plastics processors to take advantage of the opportunities offered by Industry 4.0. Even small isolated solutions provide huge benefits. From the optimisation of individual machines to the complete networking of a worldwide production pool, ENGEL is accompanying its customers on the road to the smart factory, and is continuously expanding its global sales and service teams to support the programme. "Industry 4.0 projects require very close collaboration", states Kapeller. "Short paths are an important factor in their success."
By networking production systems, the systematic use of machine, process and production data, and the use of intelligent assistance systems, the manufacturing processes in a smart factory can continuously optimise themselves. The productivity and quality of production are increasing, and at the same time, processors can respond very flexibly to ever faster changing requirements.
ENGEL categorises it’s inject 4.0 in three operational areas of the smart factory: smart machine, smart service and smart production.
smart machine
iQ weight control sold more than 1,500 timesWith production cells becoming more and more complex due to increasing process integration and automation, steering and controlling them must become that much more simple and intuitive. This is an important goal in the smart machine area. Self-adapting assistance systems play a decisive role in this. They increase process consistency and quality without requiring the machine operator to acquire special expertise.
To clearly demonstrate the functionality of these solutions, during the five days of the exhibition ENGEL will be producing inject 4.0 logos on an ENGEL emotion 80 TL injection moulding machine at its booth. The CC300 machine control is capable of simulating process fluctuations; the automatic readjustments by the intelligent assistance systems can then be tracked on the display of the machine. While iQ weight control maintains consistent injected melt volume throughout the entire injection moulding process, iQ clamp control monitors the mould breathing in order to calculate and automatically adjust the optimal clamping force.
iQ weight control was the first of the ENGEL iQ systems to enter the market five years ago. To date, it has been sold more than 1,500 times worldwide. Initially, the software was only available for injection moulding machines with electric injection units, but now hydraulic machines can also be equipped with iQ weight control. "The response in the market is excellent", says Kapeller. "iQ weight control significantly increases reproducibility in the hydraulic victory and duo machines."
Q weight control compensates for process fluctuations before rejects occur. The intelligent assistance system is available for both electric and hydraulic injection moulding machines