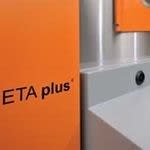
Plastics can be degraded if they are dried for too long or at excessive temperatures. ETA plus technology addresses this challenge by automatically managing the dry airflow in relation to actual demand, and by adjusting the drying temperature. The system senses fluctuations in material throughput and material temperature, and automatically adjusts airflow to the drying bin’s energy requirements. In the event of production downtime, temperature can be reduced to “standby”. This is especially important for sensitive materials. If throughput is too high, a visual warning is given.
When designing central drying stations, Motan pays particularly close attention to energy management. For example, a heat exchanger is employed during the regeneration process for its desiccant beds. This ensures that energy from hot, humid outgoing air can be recovered and used to heat the incoming air. Motan’s closed-loop cooling system, used in the cooling phase of regeneration, conserves energy by preventing the absorption of moisture before the bed switches over to drying.
Heat can also be recovered from the drying bin’s outgoing air. It can then be transferred to the dry process air via the optional heat exchanger. A thermal barrier in the drying bin prevents energy loss via the conveyer.
During waste heat recovery, energy from the return air is used to heat the cold incoming air. This also lowers the temperature of the outgoing air. Compared with conventional drying systems, those featuring ETA plus technology allow a reduction in energy consumption of over 60 per cent.
To make drying systems easier to configure, the control system is pre-loaded with a database containing the key characteristics of around 70 standard materials. Data for approximately 100 further materials can be added in accordance with customer needs.
Thanks to the winning combination of temperature adjustment, airflow control and ETA plus waste heat recovery, energy input for the drying process can be managed in line with fluctuations in drying conditions.
This provides reliable drying results, protects plastics from excessive heat exposure, and brings about a significant reduction in energy consumption. It also allows for precise temperature control, and ensures that plastic granules are neither over-dried nor insufficiently dried – guaranteeing reliable, consistent downstream production processes.
ETA plus technology virtually eliminates production errors caused by incorrect drying. The smooth interplay of all components ensures completely automated, reproducible drying processes, tailored to individual requirements and conditions.