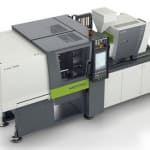
With a focus on productivity, quality and energy efficiency, Wintec builds injection moulding machines in Changzhou, China, that are tailored to the requirements of the standard market. Wintec machines are preferably used for high-volume, single-component injection moulding, which may not require any special technologies, yet still places high demands on quality and process consistency.
t-win: High degree of energy efficiency and sensitive mould protection
The hydraulic injection moulding machines of the t-win series are offered with clamping forces from 4,500 to 17,500 kN, and are thus ideal for the production of large or three-dimensionally complex components. During Chinaplas, a t-win 10500-7000 injection moulding machine with a clamping force of 10,500 kN will impressively demonstrate the performance of the series with the production of automotive interior door panels from polypropylene. The shot weight is 650 grams, each cycle takes 30 seconds.Even in the standard version, the t-win machines are equipped with the servowin servo-hydraulics, which reduces energy consumption by more than 60 percent as compared to conventional hydraulic injection moulding machines. Additional factors that contribute to a high degree of energy efficiency are the operating point optimisation and the dual-platen design of the clamping unit with low moving masses and exposed tie-bars. The linear guidance of the movable mould mounting platen reduces friction and keeps the mould area free of lubricating oil.
The dual-platen clamping unit was developed in Europe and guarantees maximum platen parallelism throughout the machine’s service life, which results in sensitive mould protection, excellent dynamics and short dry cycle times. Parallel auxiliary movements such as the ejector, core pulls, or jets, are optional possibilities.
The C2 control installed on all Wintec injection moulding machines is characterised by an intuitive operator guidance that reduces the risk of operator errors. The entire machine status is displayed on a clear-cut single screen. A quick adjustment page groups the most important setting parameters in a compact way.
In addition, the C2 offers ample flexibility in terms of connecting robots of various types and brands. As a member of the Engel Group, Wintec is in a position to deliver integrated production cells from a single source, with robots developed and produced in-house. The t-win 10500-7000 at Chinaplas is equipped with a viper 20 from Engel's linear robot series. The viper removes finished parts from the mould and places them on the conveyor belt.