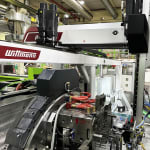
A high level of process integration and complete automation are the decisive factors to achieve the required efficiency in manufacturing fuse boxes for agricultural utility vehicles. The production equipment is flexible due to its modularity. The plastics processor Reinert describes the recently completed project as a milestone and praises the excellent teamwork with its partner companies Maier and Wittmann.
In terms of technology expertise, Reinert is certainly ahead of the game. With its focus on the automotive industry, the plastics processor can offer a remarkable range of services, including multicomponent injection molding, as well as gas injection, various insert molding techniques, clean-room production and even organo sheet processing to make light-weight parts. "We are also often in demand as development partner, especially when the task is tricky", explains Jürgen Hahn, Managing Director of Reinert Kunststofftechnik GmbH & Co. KG, during our visit to the company’s headquarters in Bissingen an der Teck, Germany - and the component lying in front of us on the table in the large conference room is certainly rather complex.
It is a fuse box for agricultural utility vehicles, consisting of two black boxes clipped together with sealing, numerous sockets and screws, plus lateral red brackets to hold the cover in place after electrical installation. "Both boxes have come out of the injection molding machine as complete assemblies including sealing and metal inserts, except for the red brackets", Christoph Klement, Deputy Project Manager at Reinert, explains proudly. "This project is really a milestone for our company."
18 variants and other products in quick succession
The challenge in this project was more than just the high cost pressure, which has long been quite common in the automotive sector, but rather the necessity to combine lowest possible unit costs with extremely high flexibility of the production cell. In fact, the fuse boxes from Reinert are produced in 18 different variants. Moreover, it was necessary to enable the highly automated production cell to be fully utilized by making some other products as well.
"That is the trend"; emphas Alen Cevra, Managing Director of Maier Maschinen- und Werkzeugbau GmbH, which is in charge of developing the integrated production process and the automation involved. "Especially here in Germany, we are more and more often dealing with a wide range of different products and consequently small batch s. This requires fast and simple machine setting processes, as well as the necessary flexibility for frequent readjustment of the production cell’s components to new requirements."
With its headquarters in Markgröningen, Germany, and another facility in the immediate neighborhood of Reinert in Bissingen, Maier specializes in the design and production of complex customized machinery and automation solutions. Maier has already supported the injection molding processor Reinert for many years in developing production equipment for extremely complex parts. "Mr. Klement came to us with a CAD drawing of the part", says Cevra. That was in the early summer of 2022. Less than one year later, the fully automated production cell had already been delivered. This success was the result of excellent teamwork between all participating companies. "The key factor is communication. We can discuss everything openly, even in the event of occasional differences of opinion, and we all know that we can rely on each other", emphas Andreas Schramm, Managing Director of Wittmann Battenfeld Deutschland GmbH, the third partner in the project. Wittmann delivered a large W832 pro linear robot, which handles the inserts as well as the finished parts and thus functions as the link between the injection molding process and the subsequent processing steps.
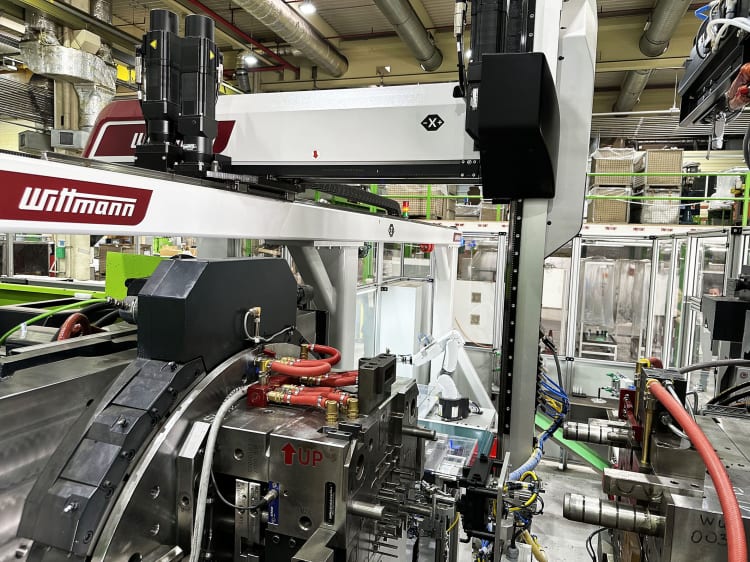
A linear robot mastering many different tasks
In spite of extensive automation, the production process now starts with manual work while the project is still at the pre-series stage. The inserts must be sorted into exchangeable trays. There are three types of inserts, which are required in different numbers for each fuse box model. Accordingly, there are three different exchangeable trays which are placed into a drawer after being filled, and are then passed on into the production cell. At that point, the robots take over. First, a small sixaxis robot chips in, whose task is to arrange the sockets and screws required for one fuse box in the specified grid dimensions. The Wittmann W832 pro takes up the inserts and places them into the lower cavity of the rotary mold inside the injection molding machine. Immediately afterwards, the gripper removes out of the top cavity the finished molded part from the previous cycle. In the 1+1-cavity mold, the base body is formed first. The hard component is a fiberglass-reinforced, flame-retardant polyamide. After rotating the mold, the second component, a TPE material, is directly molded on to provide the seal for the upper edge of the fuse box. Simultaneously, the next base element is formed inside the lower part of the mold.
Parallel to the injection molding process, the W832 pro also performs an assembly task plus a thorough quality check. From the injection molding machine, the robot first takes the part to the assembly station. In the base of the black fuse box model running off the clock-out belt on the day of our visit, there are four small holes. Later on - when installed in the vehicle - these will provide ventilation. They are now covered with a silicone membrane. To this end, the robot holds the box horizontally above the assembly station, thus enabling the rising stamp to fit the seal onto it accurately.